ASK 21 MiBaunotizen von Fredi Wiegisser, Ottoberg März - Oktober 2017 | PDF zum Download (rechte Maustaste, dann "Ziel speichern unter") |
Der Wunsch eines eigenstartfähigen Grossseglers war vor diesem Vorhaben immer noch aktuell. Und der Gedanke, einmal ein vorbildgerechtes Eigenbau Klapptriebwerk realisieren zu können,
war schon länger in meinem Kopf. So wurden beide Ideen in diesem ASK 21 Mi Projekt vereint. Um es gleich vorweg zu nehmen: Es ist mir jetzt klar, warum die meisten handelsüblichen Klapptriebwerke relativ
komplex und teuer sind. In ihnen stecken wohl wie bei mir viele hunderte Stunden Engineering Arbeit und ausgefeilte Technik, bis es anstandslos funktioniert und noch hübsch aussieht. Von der Investition her
hätte ich mir ein tolles Scale-KTW kaufen können. Nur hätte ich dann nicht die wertvolle Erfahrung bei der Entwicklung und Konstruktion damit gemacht, und da würde mir aus heutiger Sicht etwas ganz
Substanzielles im Modellbau fehlen. Und noch etwas ganz Anderes ist mir klar geworden: Ein solcher Gross-Bausatz gibt so richtig viel Arbeit und braucht Ausdauer. Ich bin froh, dass es wieder mal Platz hat
für andere Dinge in meinem Kopf, so interessant und lehrreich die Bauzeit auch war. |
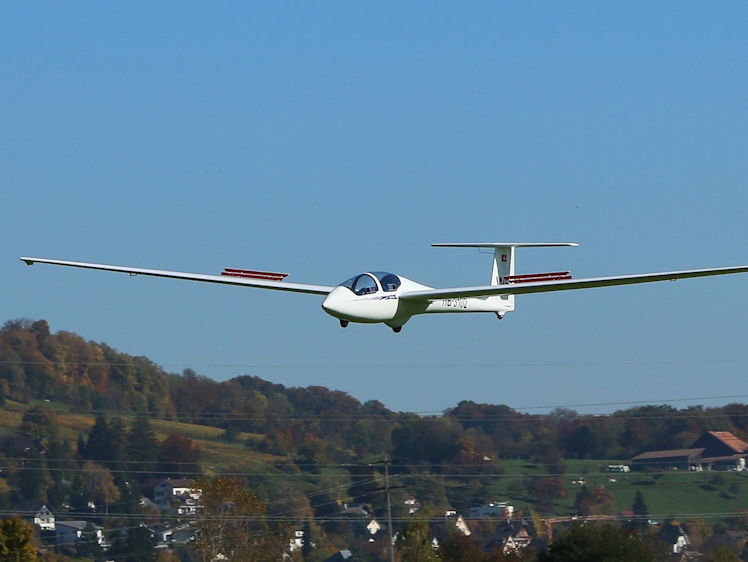 |
Bei der Modellauswahl bin ich nach vielen Gedankengängen immer wieder bei der ASK 21 von Jetisfaction hängen geblieben (Stefan Voggenreiter, Alex Braun). Der Mitinhaber Alex Braun
überführte seine gesamte Produkt- und Projektpalette aus der Alex Braun Modellmanufaktur in seine neue Modellbaufirma Jetisfaction. Darunter befand ich auch die Rumpfform der ASK 21 von
Uli Hunschok-Modellbau, auf deren Basis das Modell produziert wird. Das Festfahrwerk lädt zur Einfachheit ein, die grosse Flügelfläche und das HQ/W-2.5 Profil versprechen gutmütige Flugeigenschaften.
Ein mittelgrosser Modellmassstab gibt zudem rasch ein gut sichtbares Flugbild am Himmel her. Das grosse Bugrad scheint wie geschaffen für den KTW Selflauncher, und der breite Rumpf lädt für mein Eigenbau
Triebwerk geradezu ein. |
Aus Platzgründen (Auto, Werkstatt und Lagerung) habe ich mich für den Massstab 1:3.3 entschieden. In dieser Grösse gibt es die ASK 21 neben Jetisfaction noch die von Erwin Schreiber
mit GFK Flächen und jene von Manfred Schadl mit Styro Abachi Flächen. Die Kommunikation mit Alex war hervorragend angelaufen (WhatsApp), was sich später noch als wertvoller Bausupport mit reicher
Bebilderung herausstellte. Zufällig hatte Alex bereits Schweizer Kundschaft in meiner Nähe, und so ging ich zusammen mit meinem Vereinskollegen Jürg den Flieger anschauen und wir liessen uns die Maschine
erklären und vorführen. Die ganze Aktion überzeugte uns beide sofort, und so bestellte ich sogleich das Modell bei Alex Braun. Auf den Folgeseiten finden sich nun meine Baunotizen. |
Vertrieb DE und CH: Jetisfaction (Modell nicht gelistet, Stefan Voggenreiter oder Alex Braun anrufen) |
Flächen- und Leitwerksbau in Styro-Abachi von Tragflächen und Modellbautechnik (Stefan) Bräunig Anmerkung: Frühere GFK Leitwerke zu UH Zeiten wurden von Erwin Schreiber bezogen. |
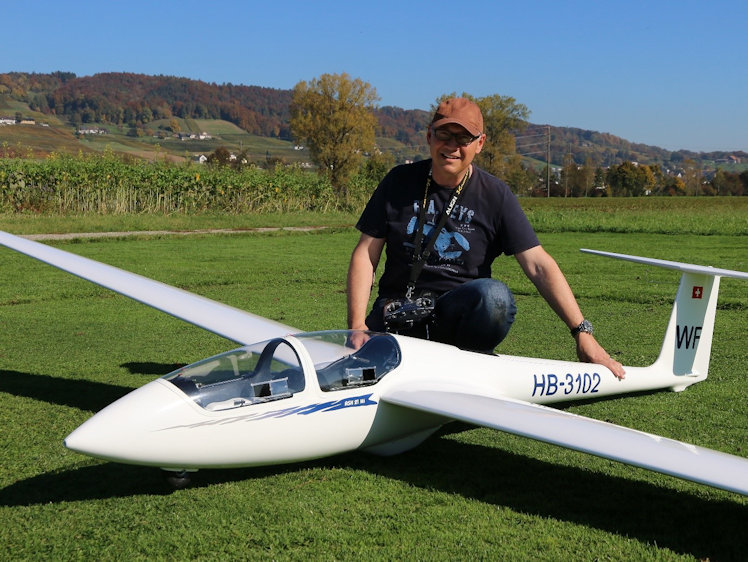 |
Bauzeit: Kontaktaufnahme mit Alex Braun: 24. März 2017 Bestellung: 25. April 2017 Anlieferung (DE Konstanz): 4. Juli 2017 Bau Fertigstellung: 15. Oktober 2017
Erstflug: 16. Oktober 2017 KTW Vorstudie bis Fertigstellung: Oktober 2016 bis Mai 2017 |
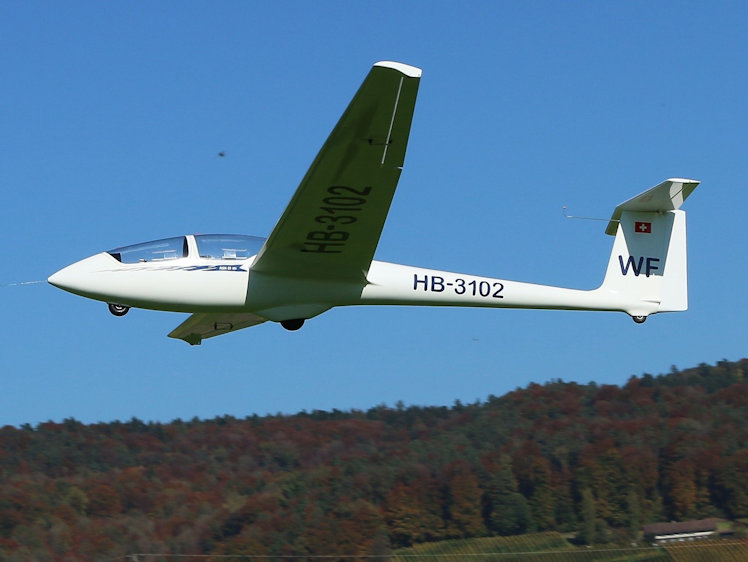 |
Modellvermessung:
- Modell mit guter Form- und Massstabtreue.
- Spannweite 5.15m, jedoch geliefert ohne Randbögen (Original 17.0m)
- Rumpflänge 2.54m, SLW ist 1cm zu lang (Original 8.35m)
- Rumpfbreite 0.225m (Original 0.75m)
- Hauptrad DU-BRO 102mm oder bei Verwendung einer Bremse FEMA 102mm (Orig. 5“ – 340mm)
- Bugrad DU-BRO 83mm – etwas zu klein (Orig. 4“ - 290mm)
- Spornrad DU-BRO 57mm – etwas zu klein (Orig. 2.5“ – 210mm)
- Flügelrad 24x6mm (Orig. 80x15mm)
- Rumpf Rohbau mit Haubenrahmen 2‘035g, nach Vollausbau mit Leitwerken und Steckung 9‘750g
- Steckung CFK/Alu 695x25mm, 655g
- Fläche links Rohbau 2'460x465/165mm, 2'493g, nach Vollausbau 2‘925g plus Randbogen 35g
- Fläche rechts Rohbau 2'460x465/165mm, 2'555g, nach Vollausbau 2‘955g plus Randbogen 35g
- Fläche rechts rund 60g schwerer, und die Kontrolle zeigt eine langsame Rollrichtung nach rechts.
- Fläche rechts nach Vollausbau nur noch rund 30g schwerer, beim Bauen 30g kompensiert.
- V-Form der Fläche = 2x 2.7° = rund 5.4° (Orig. ca. 2x 3.5° = 7.0°)
- Profilwölbung 10.5mm (ca. 2.3%), Profildicke 60.0mm (ca. 12.9%), Profil annähernd HQ/W-2.5/13
- Realer Profilabdruck ist ab der Steckung nach hinten minim nach unten «verschoben» gegenüber dem Original HQ/W-Profil. Ein verrutschter Profilabdruck schliesse ich aus, weil sich der Endleistenpunkt im Vergleich wieder deckt. Zudem ist die Profilkontur vor allem im Holmbereich minimal unstetig, jedoch alles solide Handarbeit.
- Nullauftriebswinkel α0 ca. -3.5° für mittlere Re und N=11 gemass Literatur Helmut Quabeck.
- Geometrischer Anstellwinkel αg ca. +3.5° gegenüber gemittelter Rumpfachse.
- Demzufolge im horizontalen Geradeausflug betragt der effektive Auftriebswinkel α ca. 7.0°
- HLW Rohbau 980x245/125mm, 356g, nach Vollausbau 407g
- SR Rohbau 420x140/90mm, 86g, nach Vollausbau inkl. 2mm Stahldraht 114g
- Bremsklappen Schambeck 450mm Ausfahrhöhe 57mm
- Modell Leergewicht im Rohbau bei Anlieferung 8‘364g
- Modell Abfluggewicht nach Vollausbau 15‘700g
- Modell Werkslackierung RAL 9016
- Packmasse bei Anlieferung 2510x555x470mm, 21.1kg
|
KTW Bau:
- Für das ASK 21 Mi Projekt kamen nur die semi-scale KTW von LET, EMS und Elicker in Frage, weil alle anderen Typen der Optik für dieses Projekt untreu sind und
keinen 2-Blatt Starrprop haben. Sie alle haben jedoch eines gemeinsam: Einen überaus stolzen Preis. Mit Hilfe von RCN Berichten und Modellbaukollegen entwickelte
ich ein semi-scale KTW mit dem Ziel „Alles um 1000“, welches folgende Eigenschaften aufweisen musste:
- Geringes Gewicht um 1‘000g (für ein 18 Zöller um 1‘800W)
- Günstiger Preis um 1‘000.-
- Skalierbarkeit für grössere und kleinere Modellmassstäbe (ca. 16 bis 20 Zoll)
- So hatte ich im Herbst 2016 mit einer KTW Studie begonnen. Ziel dieser Studie war die Einfachheit, die Skalierbarkeit das Gewicht und den Preis in den Griff zu
bekommen. Glücklicherweise stellte mir Alex Braun ein defektes Rumpffragment des Modells zur Verfügung, mit welchem ich meine KTW Ausschnitte nach Belieben üben
konnte und nachprüfen konnte, ob alles zum Passen kommt. Besser geht’s nicht mehr! Dieses Fragment hatte ich solgleich für die Abformung meiner KTW Klappen benutzt,
sowie den direkten Klappenausschnitt ohne die vorausgehende Rumpfabformung erprobt.
- Die Berechnung ergaben ein KTW 18“ Eigenbau, GFK 3mm. Eingangsleistung 1‘830W, Akku 10S
- Prüfstand Lasttest hier
|
Probleme beim KTW Bau:
- Bei Vollgas ist die Turmtorsion und die Vibration problematisch. Mit 3mm GFK gut reduziert. Es braucht aber einen 2. Turmspanten im Rücken, um die Schwingung genügend zu dämpfen.
- GFK Dickentoleranzen der Platten ist problematisch, um +/-- 10% ist normal. Schlitze und Verzahnungen deshalb 3.4mm gewählt.
- Die Power ist eine Herausforderung an die Konstruktion, Turmmoment mit rund 2‘400Ncm und Turmanschläge entsprechend 120kg je Seite. Das muss alles halten!
- Beim Test ging der Stator des guten Hacker Getriebemotors nach hinten los. Allenfalls sind nicht die etwas überdimensionierten 10S daran schuld, sondern eher der fehlerhafte RotorStar Regler (allenfalls Fehlkommutierungen).
- Beim Folgetest ging der RotorStar Regler in Rauch auf (aktueller Motor bereits Leomotion L4031)
- Beim Folgetest YGE mit Leomotion vibrierte der Turm ab 30A (max. wäre 47A).
- Beim Schlusstest mit dem 2. Turmspant im Rücken konnte ein Erfolg verzeichnet werden.
- Anschliessend viele weitere Verbesserungen in der Mechanik vorgenommen.
|
Rumpfabformung für KTW Klappen:
- Trennwachs nicht mit Pinsel auftragen, das gibt Striche die nicht wegpoliert werden können.
- Trennwachs mit Baumwolltuch auftragen und jede Lage einpolieren. Nicht zu viel Material pro Durchgang auftragen.
- Anleitung für Form erstellen und Klappen abformen, oder alternativ KTW Klappen direkt ohne Form aus Rumpf ausschneiden.
|
Antriebsstrang:
- Leomotion 4-pol Innenläufer L4031-1400 mit Getriebe 6.7:1 (1'380 U/V) ca. 360g
- Mejzlik 2-Blatt CFK 18x10“ E-L noch nicht weiss lackiert 31g
- Leomotion Spannkonus Welle 6mm Mitnehmer 8mm Gewinde gekürzt 25g
- YGE Regler 90 HV V5 Opto 80g
- Zippy Compact Akkus LiPo 10S / 4‘500mAh / 35C 1‘125g
- Strom 47A @39V (Sommer 30°)
- Eingangsleistung 1’830W
- Drehzahl ca. 8‘033 U/min (errechnet, nicht nachgemessen)
- KTW Gewicht mit allen Kabeln ohne Akkus und Regler 1‘074g
|
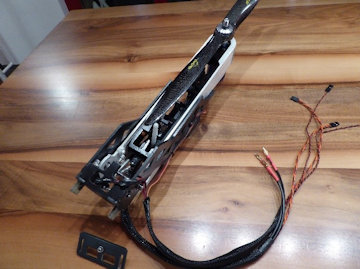 | 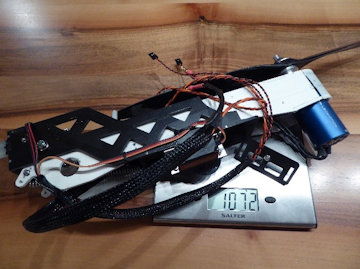 |
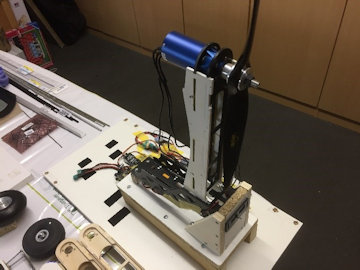 | 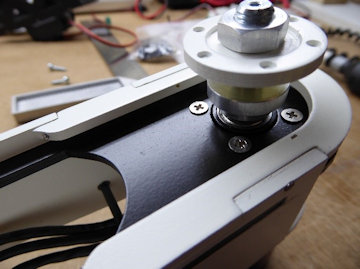 |
KTW Version v1.0 noch als Prototyp |
Schleppkupplung einbauen:
- Lage nicht unten wie beim Original gemacht, sondern in der Spitze wo das Pitot-Rohr steckt.
- Ist bequemer zum Einhängen und sieht aus als wäre eine Pitot-Rohr Aufnahme verbaut.
- Leibung bei der öffnung hergestellt, SK ist etwas zurückversetzt und soll unauffällig bleiben.
- Leibung ca. 10mm tief mit eingedicktem L-Harz hergestellt.
- Loch 9mm gebohrt (Achtung Rumpfnaht ist nicht zentriert). Eigentlich müsste das Loch ca. 12mm sein (Original wäre ca. 40mm), die SK hat aussen aber nur knapp 12mm und innen noch 10mm.
- Spezialwerkzeig erstellt und mit Proxxon von innen ein Sackloch 12mm für die Schleppkupplung geschliffen, bis die Leibungsdicke noch ca. 5-6mm beträgt.
- SK eingesetzt und ausgerichtet und mit 5min Epoxy fixiert (was aber nicht wirklich gut fixiert hat, habe wohl zu wenig Harzgemisch erwischt).
- Dann mit eingedicktem L-Harz weiter eingeharzt bis die SK gut bedeckt ist (Achtung dass die Mechanik später nicht ansteht oder verklebt).
- Spez. Servohalter mit eingedicktem L-Harz eingebaut, Gewindestange M2.5
|
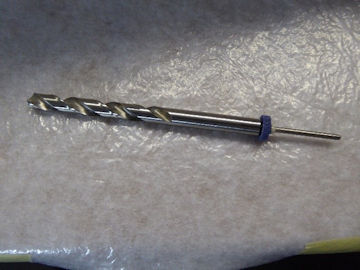 | 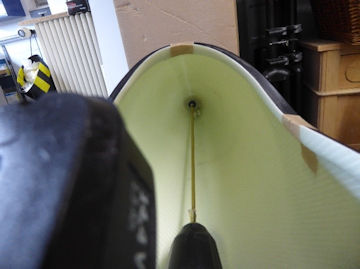 |
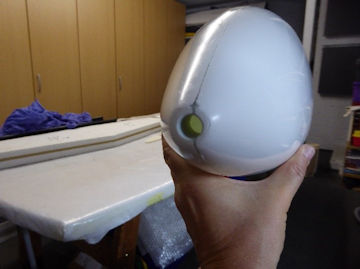 | 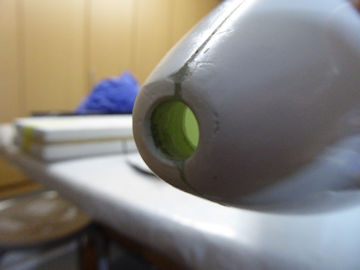 |
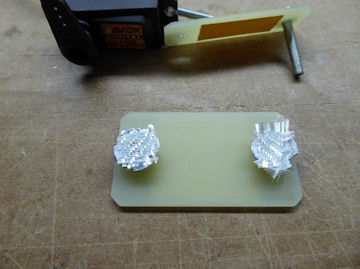 | 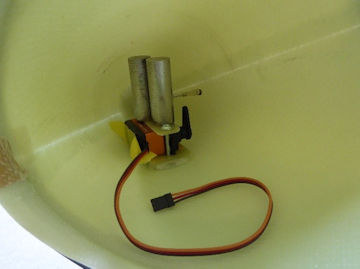 |
Fahrwerk einbauen:
- Festfahrwerk mit DU-BRO 102mm Hartschaum Rad ist werkseitig ungedämpft und ungebremst geliefert.
- Ich will zur Not bremsen können und rüste das FW mit Radbremse aus (Eigenkonstruktion). Ich nehme dazu ein FEMA 102mm Vollgummi Rad, das hält länger auf Bremswirkung als das DU-BRO Rad. Bis es da ist, bohre ich die Platten und die Radnabe auf 6mm auf, damit es später passt.
- Die Holzspanten und Aluplatten sind asymmetrisch, lange Schenkel nach hinten, kurze Schenkel nach vorne.
- Holzspanten mit GFK Radkasten Innenseite verharzen. Danach Aluplatten auf Innenseite Holzspanten halten und Schenkelspitzen 1mm über GFK Radkastenrand herausragen lassen (1mm entspricht ca. Rumpflaminatstärke) und die 6 Löcher anzeichnen und bohren. 6 Schrauben M5 von aussen durch den GFK Radkasten und durch den Holzspanten in die Aluplatte drehen, vorgängig Gewinde M5 in Alu schneiden.
- Radkastenöffnung im Rumpf rechteckig vornehmen, etwas kleiner als der GFK Radkasten. Radkasten ausrichten und rundum einharzen.
- Radverkleidung unten öffnen und seitlich mit je 3 Schrauben montieren, vorne und hinten je 1 Schraube.
- Fahrwerkbremse 2 Lagerbolzen M6x35mm, darf nicht durchgehend sein, sonst im Rumpf nicht mehr demontierbar! Wellen am Ende 2x flach geschliffen für 4 Madenschraube M3. Ein Lagerbolzen zusätzlich mit stirnseitigem M3 Gewinde für Servohebel. Aluklemmhebel wäre wohl einfacher und dauerhafter (und teurer). Bremsklotz Alu 10mm dick, ca. 30x20mm. Bremsservo auf Servohalter wie bei Schleppkupplung.
|
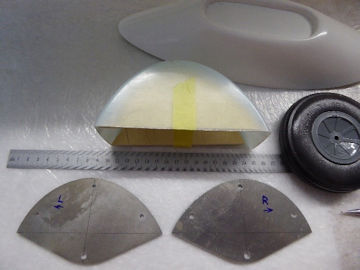 | 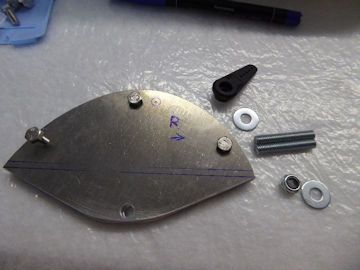 |
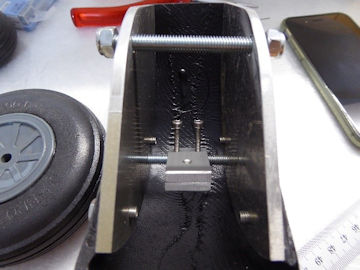 | 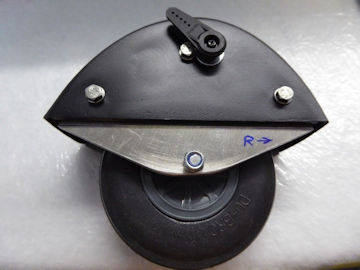 |
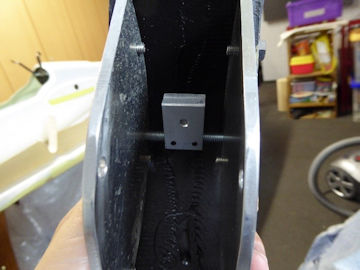 | 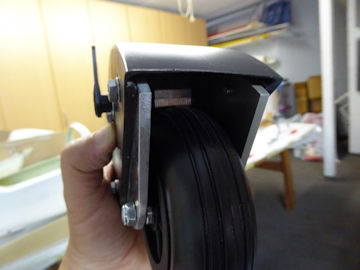 |
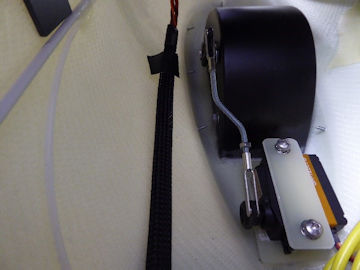 | 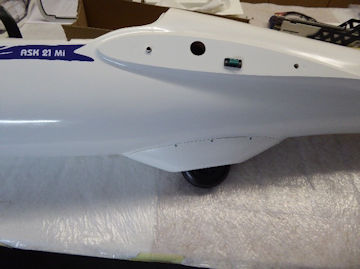 |
Bugrad einbauen:
- Bugrad DU-BRO 83mm aus Hartschaum ist werkseitig mitgeliefert. Leider etwas zu klein, 87-88mm wären besser. Dann passt der Radkasten aber nicht mehr, und die Bugradöffnung würde fast an der Rumpfmanschette anstehen. Also nehme ich das gelieferte 83mm Rad.
- Radkasten ist sehr eng, nur 1mm Spiel zwischen Radkasten und Rad, wenn das Rad zentriert ist.
- Verstärkung für M4 Radachse mit 2mm GFK Platten als halbrunde Achsenaufhängung hergestellt, auf der Radkasten Innenseite seitlich eingeharzt und mit 2 M3 Schrauben zusätzlich verschraubt. Achsaufhängung ca. 32/8mm mit Bohrung 4mm, Schenkel etwas verlängert.
- Optik wie beim Original mit sichtbaren Stoppmuttern ausgeführt.
|
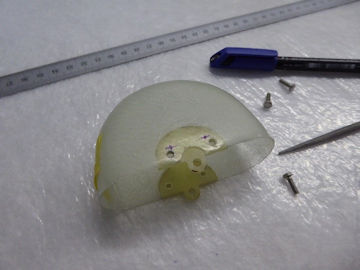 | 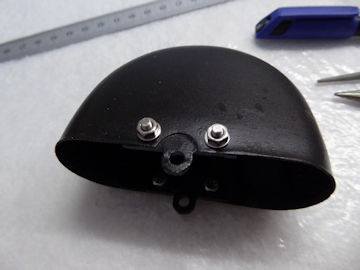 |
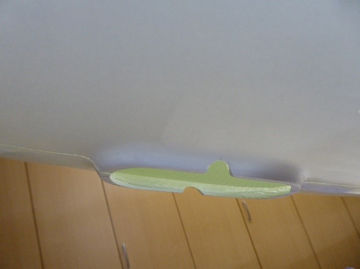 | 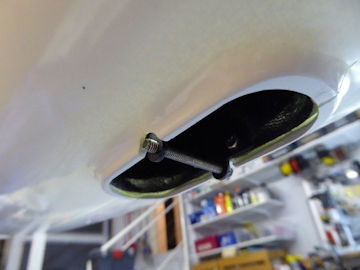 |
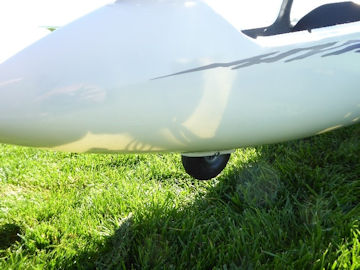 | 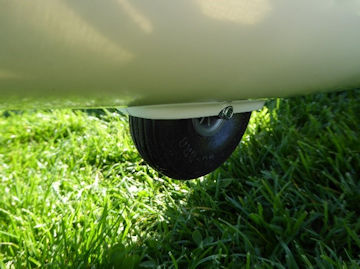 |
Holmbrücke einbauen:
- Schablone der Wurzelrippe liegt dem Bausatz bei. Diese je an eine Flächen halten und Steckung durch die Schablone hindurch in die Fläche schieben. Resultat: Schablonenprofil ist minim zu dünn, nur die obere Profilkontur der Schablone ist mit der Fläche bündig. Und Nasenleiste der Fläche steht ca. 1.5-2mm über die Schablone. Beides habe ich beim Anzeichnen berücksichtigt.
- Kontrolle ob beide Anstellwinkel am Rumpf gleich sind. Hierzu SLW und Tischauflage mit Senklot ins Lot bringen, dann Profilsehne herausmessen. Resultat: Die Höhendifferenz der Profilsehnen beträgt ca. 2mm (rechts liegt sie tiefer als links), und die Anstellwinkeldifferenz der Profilsehnen beträgt rund 0.1° (rechts minim flacher als links). Hierzu unternehme ich nichts, die Bau- und Pilotenfehler sind sicher grösser als diese Unregelmässigkeit.
- Steckung mit Trennwachs einpoliert, Holmbrücke mit eingedicktem 5min Epoxy ausgerichtet und fixiert. Trennwachs später wieder entfernt.
- Kontrolle der Holmbrücke mit aufgesteckten Flächen, passt soweit gut und ist Top waagrecht geworden. Die vorgemerkten Korrekturen waren prima. Flächen aufschieben geht extrem streng. Tipp von Alex befolgt: 3mm Entlüftungslöcher unterseitig gemacht, und Rohr innen vorsichtig ausgeschliffen (800er Körnung) und herausgeputzt.
- Der Furnierüberstand der Flächen muss natürlich noch angepasst werden (siehe Flächen an Rumpf anpassen). Der Flächenspalt ist werkseitig bedingt vorhanden und ist kein Baufehler (erst dachte ich der Holm sei etwas gegen den Uhrzeigersinn verdreht eingebaut). Bei mir war der Spalt links vorne 2mm und rechts hinten 4mm.
- Holmbrücke wird jetzt endfest eingeharzt.
- Torsionsplatten Löcher auf 8mm aufgebohrt und mit aufgesteckten Flächen endfest eingeklebt.
|
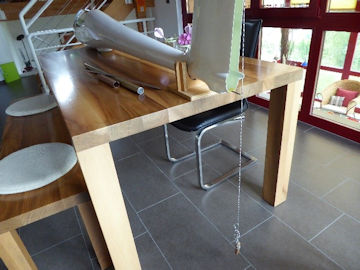 | 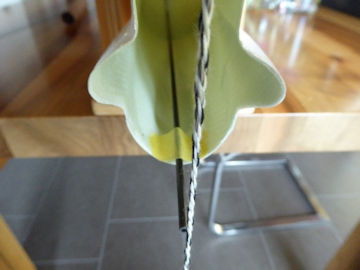 |
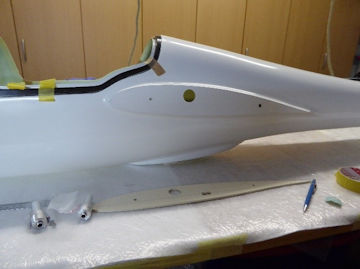 | 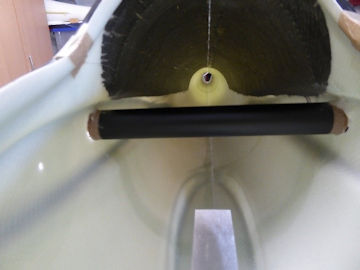 |
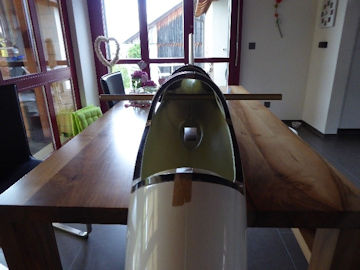 | 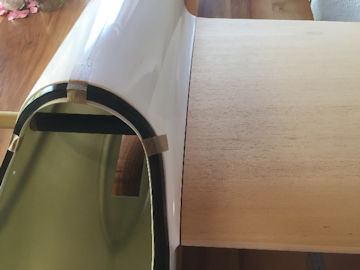 |
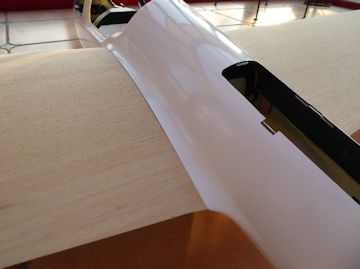 | 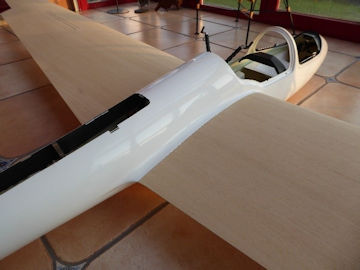 |
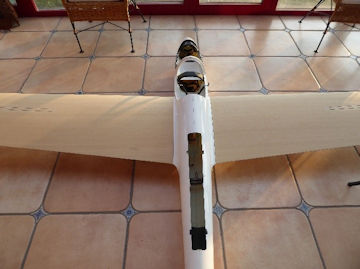 | 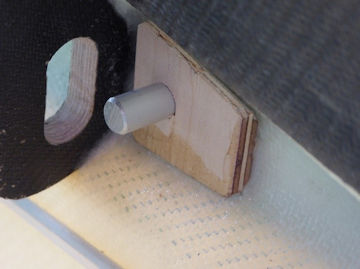 |
Seitenleitwerkspanten einbauen:
- Rumpf auf den Rücken legen, zuerst den kleinen Top-Spanten eingeharzt. Mit eingedicktem Harz ca. 10-15mm dick unterfüllt (hinten 15mm gemessen, Wölbungshöhe der Auflage ca. 4mm). Später werden die 2 Gewinde für das HLW direkt in den Aufbau geschnitten. Es hat sich herausgestellt: 15mm ist etwas zu viel Material, das braucht es nicht. Und der Servohebel steht später nur am Material an. 10mm würden auch gut reichen.
- Nach dem Austrocknen zuerst EWD festlegen (siehe EWD festlegen) und die 2 Gewindelöcher M5 für das HLW bohren, danach zwischen den Schraubenlöchern die öffnung für das Servo ausdremeln. Um die EWD setzen zu können, passe ich zunächst die Flächen an (siehe Flächen an Rumpf anpassen).
- Das HLW hat Markierungen für die 2 Befestigungsschrauben, in diesem Bereich ist das HLW komplett mit Holz unterfüttert.
- Die 4 Gerüstspanten müssen im SLW drin zusammengesetzt werden, sonst kann es nicht eingeschoben werden. Die Aussparung für die SR-Anlenkung habe ich nach rechts genommen.
- Vor dem verharzen des Gerüstes die Hohlkehle seitlich schiften, damit die Endkanten des SLW parallel zum Kehlenspant verlaufen. Ich habe Balsaplättchen verwendet unten ca. 2mm mittig ca. 1.5mm und oben noch ca. 1mm dick.
- Mit langem Stäbchen oder Röhrchen das Harzgemisch in die Fugen bringen. Hierzu habe ich fast 2h Zeit benötigt, da die Zugänge teils sehr schlecht sind.
|
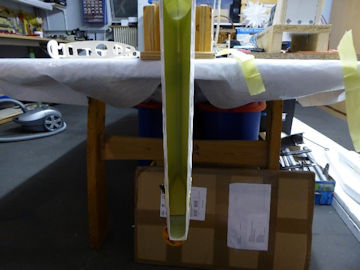 | 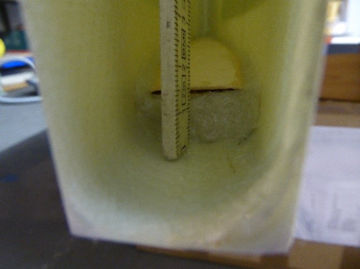 |
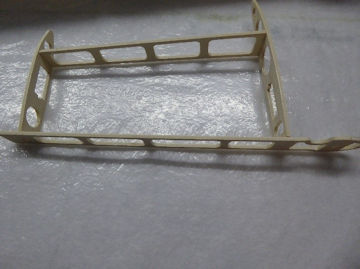 | 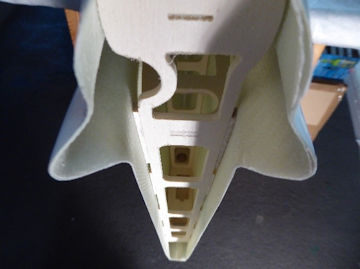 |
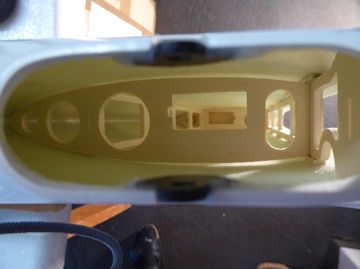 | 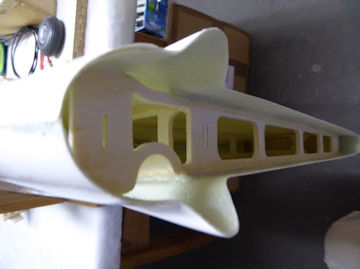 |
Spornrad einbauen:
- Spornrad DU-BRO 57mm aus Hartschaum ist werkseitig mitgeliefert. Leider etwas zu klein, 63-64mm wären besser. Dann würde aber die Spornradöffnung fast an der Rumpfmanschette anstehen. Also nehme ich das gelieferte 57mm Rad.
- Verstärkung für M4 Radachse mit 2mm GFK Platten als halbrunde Achsenaufhängung hergestellt, und auf die Rumpf Innenseite eingeharzt. Zur Ausrichtung der Achsenaufhängungen die Radachse durchgeschoben und die lichte Weite mit 2 Kontermuttern eingestellt. Achsaufhängung ca. 16/8mm mit Bohrung 4mm, Halbkreis ca. 2mm zurückgestuft und als Kreissegment ausgeführt (Schenkel konnten nicht verlängert werden wie beim Bugrad, sonst wäre entweder die Achse zu weit hervorgestanden oder der Halbkreis würde an der Radfelge anstehen.
- Optik wie beim Original mit sichtbaren Muttern mit Sicherungslack ausgeführt. Stoppmuttern wären zu hoch und sehen für meinen Geschmack weniger gut aus.
|
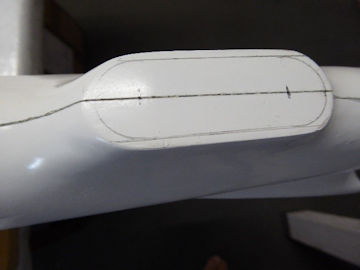 | 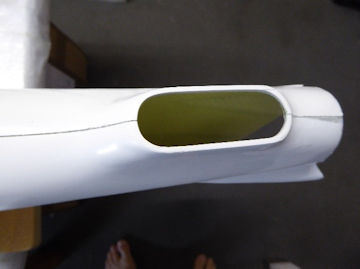 |
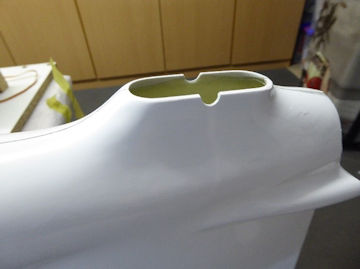 | 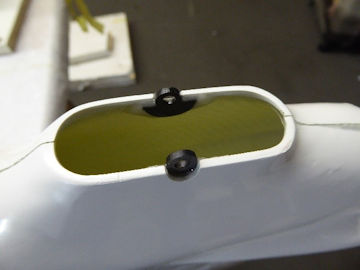 |
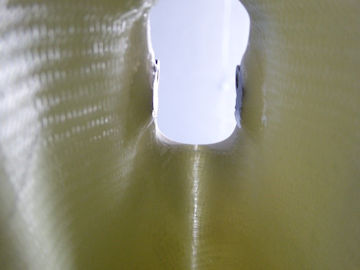 | 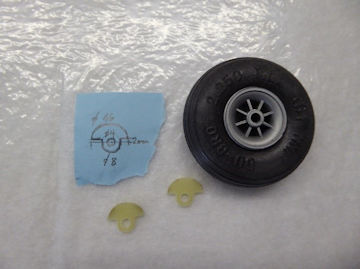 |
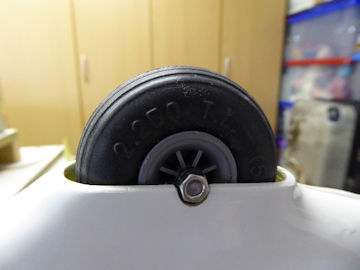 | 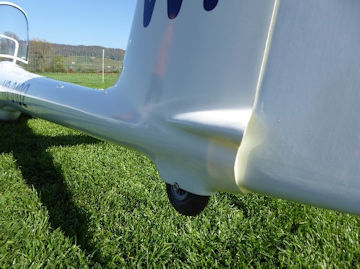 |
Seitenruder einbauen:
- Durchgehender Bowdenzug für 2mm Stahldraht als Scharnieraufnahme werkseitig geliefert.
- Aufhängung oben: Nylon-Clip Schnellverschluss. Aufhängung unten: Alu Bolzen entweder für 2mm Stahldraht oder für M3 Gewinde mit Schraube von unten. Ganzes Kit von EMS Manufaktur.
- Halbrunde Wurzelleiste bis auf ca. 2mm komplett in Hohlkehle versenkt. Ruderausschlag ca. +/- 40mm, dann steht das SR an der Finne an. Ich hätte die Finne im unteren Viertel wohl nochmals 1mm je Seite mehr aufspannen müssen (siehe Seitenleitwerkspanten einbauen), um 2x 5mm mehr Ruderausschlag zu erhalten. Allerdings wäre dann sehr grosse Spannung drauf, und tendenziell verzieht sich dann das SLW. Also lebe ich mit dem SR-Ausschlag, den ich habe.
- Balsaauflagen für die Aufhängungen, Holzporen mit Sekundenkleber verschlossen und Auflage nachgefeilt, bis das SR schön läuft.
- Leider ist das SR werkseitig 1cm zu lang und vor allem etwas zu wenig hoch nach Oben hin geraten. Keine Kritik ans Werk, nur eine Notiz. Die lange Seite misst ca. 41.5cm statt ca. 43cm, das heisst es ragt nicht wie beim Vorbild über das Höhenruder hinaus. Durch meine positive EWD Auflage des HLW wirkt es optisch erst recht zu kurz, und das Top des SR verschwindet komplett im HR. Das wurde mit einem 1.5cm Balsaaufsatz auf dem Top des SR korrigiert.
|
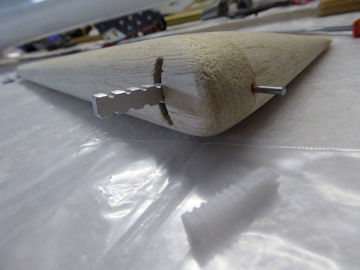 | 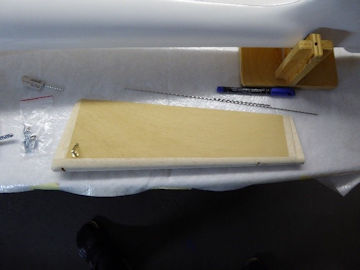 |
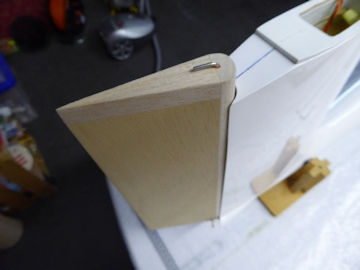 | 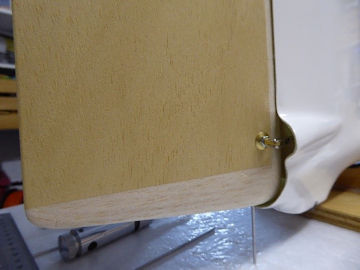 |
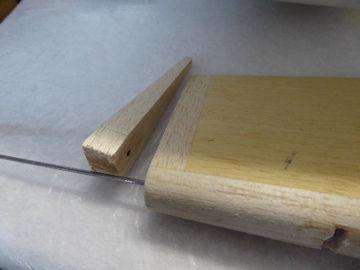 | 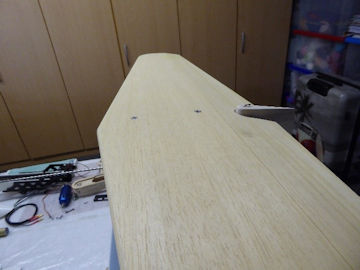 |
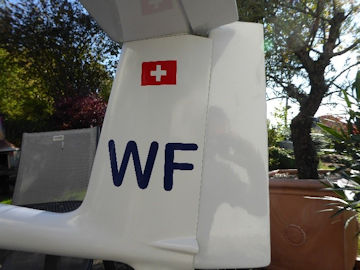 | 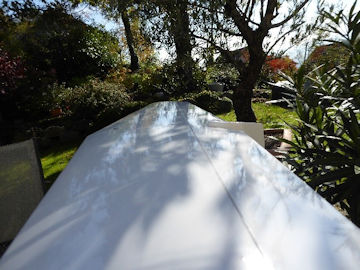 |
Flächen an Rumpf anpassen:
- Der Furnierüberstand der Flächen muss der Rumpfanformung angepasst werden. Ein Flächenspalt ist werkseitig bedingt vorhanden und ist kein Baufehler (erst dachte ich der Holm sei etwas gegen den Uhrzeigersinn verdreht eingebaut). Bei mir war der Spalt links vorne 2mm und rechts hinten 4mm.
- Zu kürzender überstand auf Flächen anzeichnen und mit langem Schleifklotz abnehmen, bis es passt. Beim 4mm überstand rechts vorne (resp. 4mm Spalt rechts hinten) zuerst ca. 2mm mit Fein Oszillatorsäge abgetrennt, gibt weniger Schleifarbeit.
- Torsionsstifte 8mm einbauen > die Torsionslöcher der Wurzelrippen passte an dieser Stelle nicht gut auf die Schablone, der Lochversatz beträgt rund 2mm. Weil das Torsionsloch im Rumpf schon mittels Schablone gebohrt ist, korrigiere ich den Versatz an der Wurzelrippe. Das Torsionsloch muss dort ohnehin auf 8mm aufgebohrt werden.
|
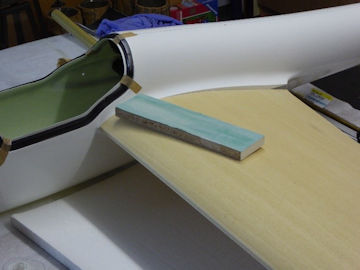 | 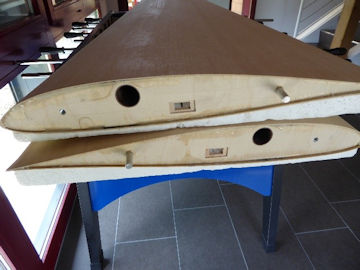 |
EWD festlegen:
- Herstellerangaben: 1.5° für beste Thermikeigenschaften, 1.0° für Kunstflug geeignete Anwendung. Ich wähle 1.3°.
- Profilsehne der Flächen auf 0° horizontal bringen. Rollachse parallel zum Messtisch bringen. Gierachse der Tischlänge nach ausrichten. HR mittels 2 Peilhölzer auf Neutral setzen.
- Meine Ausmessungen haben ergeben, wenn die Scharnierlinie des HR direkt über der Absatzkante des SLW liegt, ist die EWD ca. 0.7°. Eine Verschiebung des HLW auf der Finne um 1mm ergibt eine EWD änderung um ca. 0.07°.
- Für kleinere EWD unter 1.2° kann man durch verschieben des HLW die gewünschte EWD einstellen (Vorgehen entspricht der Hersteller Empfehlung). Bei grösseren EWD’s ist zu bedenken, dass dann die HLW Auflage ggf. nicht mehr ganz so gut passt, und der Abstand der Nasenleiste zur SLW Kante ggf. optisch etwas zu kurz wird.
- Für 1.3° EWD würde ich eine HLW-Verschiebung um fast 9mm nach hinten benötigen. Hinzu kommt vorne ein Profilsehnensturz um 0.2° gegenüber der Rumpfanformung auf Grund kleiner Bauungenauigkeiten. Also müsste ich das HLW insgesamt um fast 12mm nach hinten rücken, was keine ideale Auflage mehr gibt und mir optisch auch nicht mehr so gut gefällt. Ich bringe deshalb die Scharnierlinie des HR über die Absatzkante des SLW und schifte die Auflage von vorne nach hinten mit 0.3mm Birkensperrholz. Danach stelle ich die öffnung für den Servoschacht her.
|
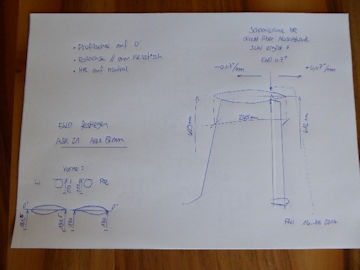 | 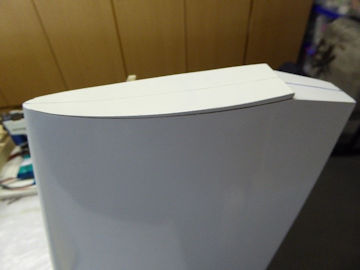 |
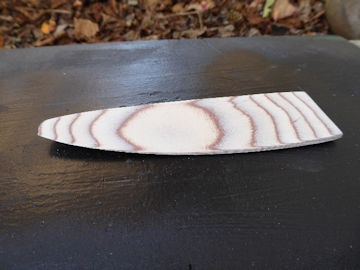 | 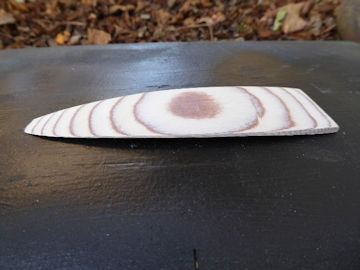 |
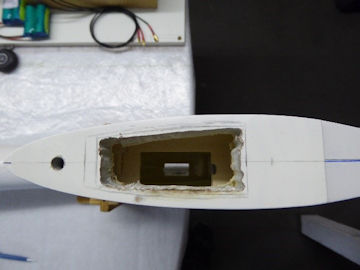 | 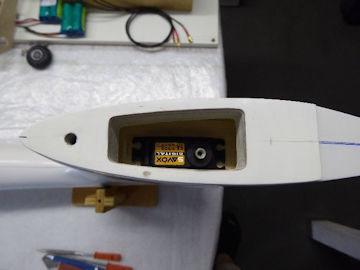 |
Höhenleitwerk einbauen:
- HLW mit verlängertem Anschlagwinkel der Rumpfachse nach 90° ausgerichtet.
- M5 Gewinde für die Befestigungslöcher in die Harz-Baumwoll-Unterfütterung geschnitten und mit dünnem Sekundenkleber überdeckt, dann das Gewinde nochmals nachgeschnitten.
- HR für SR ausgespart und Schnittfläche mit dünnem Balsa neu verklebt und verschliffen.
- Werkseitig ist das mitgelieferte GFK Ruderhorn vorgesehen, welches durch einen kleinen durchgehenden Schlitz mit der unteren und oberen Planke beidseitig mit UHU Endfest 300 verbunden wird. Da meine Anlenkung aber schräg um die M5 Befestigung herum und schräg nach oben zum Ruderhorn hinführt, müsste ich das Ruderhorn etwas verdreht einbauen, das gefällt mir nicht. Ich nehme eine M4 Augenschraube
und verdrehe sie. Allerdings ist die zugehörige Hülse zu kurz und ich kann sie nicht mit der oberen Planke verbinden. Also setze ich ein Stück Birkensperrholz ein (Verbundfläche 28x18mm) zur Unterfütterung und Verbindung der beiden Abachiplanken. Darin hält die Hülse der Augenschraube bombenfest, die Kräfte werden besser verteilt, und das ohnehin schon wegen der Seitenruder Aussparung geschwächte
HR wird erst grad noch in dem Bereich verstärkt, 2 Fliegen auf 1 Schlag.
- Jetzt rächt sich das zu viel unterfütterte Material beim Punkt Seitenleitwerkspanten einbauen. Das HR Gestänge steht an der Unterfütterung an, ich muss viel Material ausfräsen und zudem aufpassen, dass das hintere M5 Gewinde des Höhenleitwerks komplett in Takt bleibt. Viel Arbeit.
|
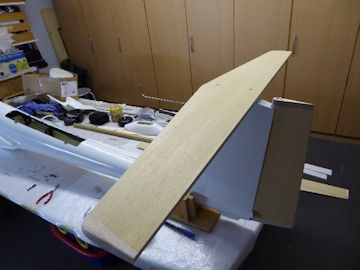 | 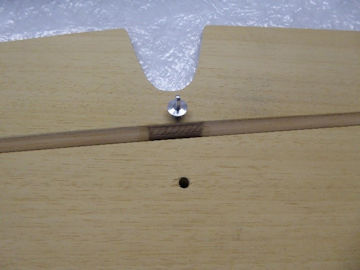 |
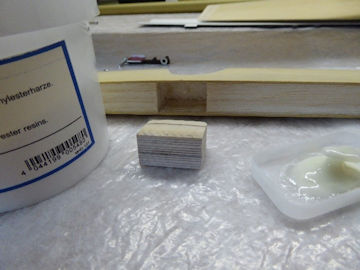 | 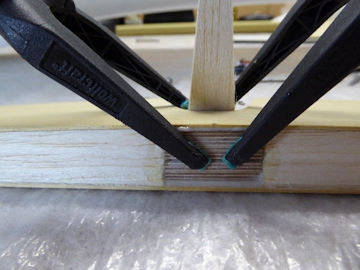 |
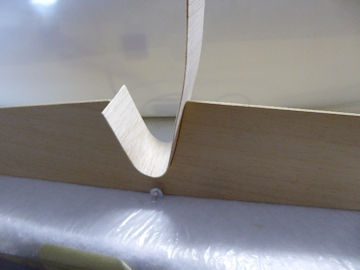 |  |
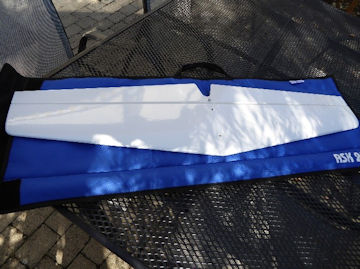 | 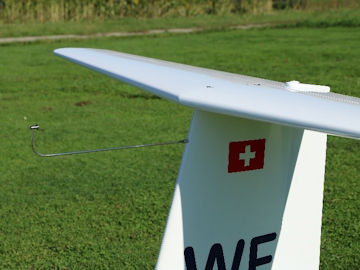 |
Klapptriebwerk einbauen:
- Eigene Einbauanleitung befolgen: Anfangsposition der Klappen 240mm hinter Cockpitkante. Das ist weit hinten, aber das ist scale.
- Klappenausschnitt mit Schablone auf Rumpf übertragen. Endmasse sind 70x60x545mm
- Alumassstab angeschlagen und mit Fein Oszillationssäge die geraden Schnitte mit 0.5mm Spalt gemacht.
- Scharnieraussparungen mit 0.5mm Kleinsägeblatt und Rundungen mit 0.5mm Dremelbohrer gemacht.
- Auf diese Weise konnte ich den herausgetrennten Klappensatz direkt gebrauchen, obschon ich vorsorglich den Rumpf für die KTW Klappen abgeformt hatte. Ich brauchte die Form jedoch nicht.
- Achtung sichtbare Rumpfnaht ist im KTW Bereich ca. 2.5mm aus der geometrischen Mitte nach links verschoben. Der KTW Unterbau muss also um dieses Mass versetzt in den Hauptspanten montiert werden. Dies musste bei der Spantenkonstruktion berücksichtigt werden.
- Spantensatz einpassen, KTW am Hauptspant anschrauben und ganze Einheit in allen 3 Achsen ausrichten, Spant einharzen. Achtung Turmneigung vorab einstellen (ich habe rund 2° rücklagige Neigung ggü. Profilsehne), dann ca. 2mm Spalt zwischen Turm und KTW Schacht belassen.
- 3 Achsen ausrichten: Darauf achten, dass die Oberkante des KTW Unterbaus parallel verläuft zur Klappenkante im vorderen Bereich (Nick), dass der Turm links und rechts vom Schacht den gleichen Abstand hat (Gier) und dass der Turm senkrecht auf dem Rumpf resp. fluchtend zum SLW steht (Roll). Die Einbauhöhe des Unterbaus habe ich so weit wie möglich nach oben gesetzt.
- Die in Längsrichtung konkaven Klappen hakelten beim öffnen vorne und hinten beim Rumpf ein. Spaltvergrösserung auf 1mm, Kanten abrunden und Scharniere mit weniger Spiel brachten keinen Erfolg. Problem erkannt: Der Scharnierdrehpunkt liegt unterhalb der Ausschnittkante und
bewegt die Klappen nicht nur nach oben sondern auch seitlich zur Ausschnittkante hin. Lösung: Ein drittes „fliegendes“ Scharnier mit 0.3mm CFK Folie in der Klappenmitte angebracht, welches während der ganzen Drehbewegung an der Rumpfausschnittkante anliegt und die Klappe quasi „zurückhält“. Dadurch wird während des öffnungsvorgangs eine in Längsachse konkavere Klappenkrümmung erwirkt, und die Klappenenden erhalten so mehr Abstand zum Rumpfausschnitt.
- Klappenantrieb: Zwei 9mm Servos im hinteren KTW Spant, 2mm Stahldraht und Gabelkopf M2, abgesägte Augenschrauben auf Klappen geharzt
|
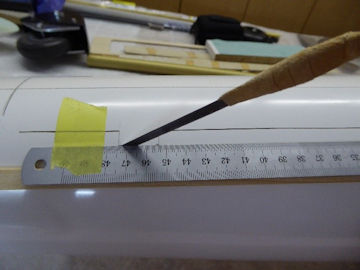 | 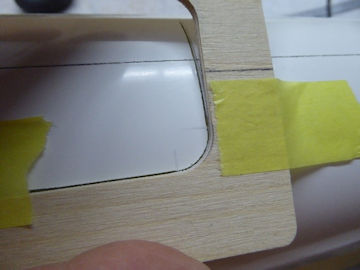 |
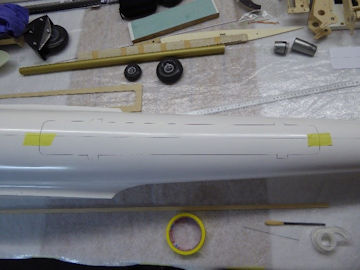 | 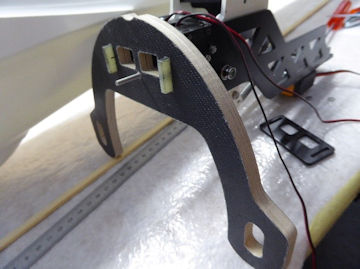 |
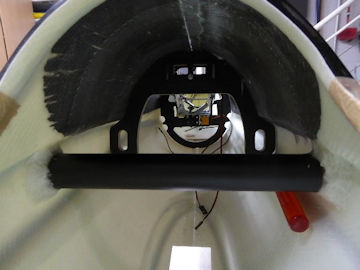 | 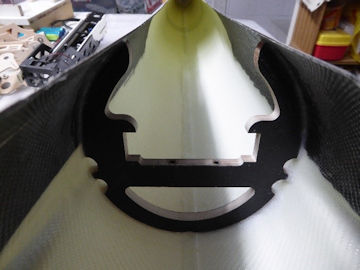 |
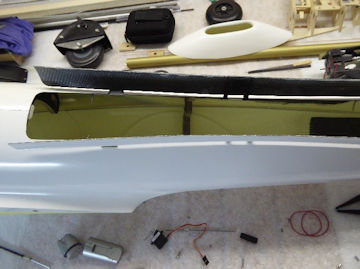 | 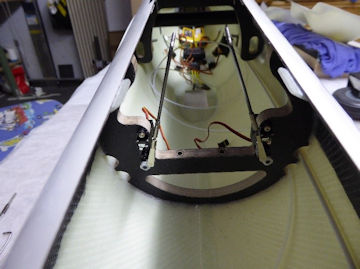 |
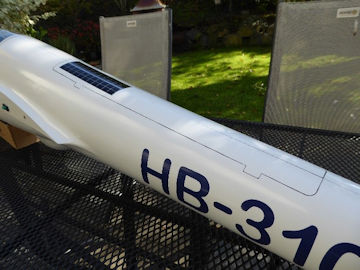 | 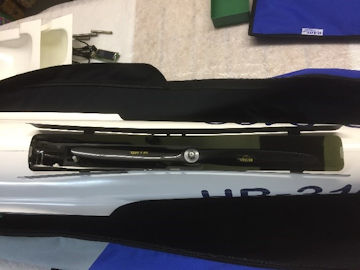 |
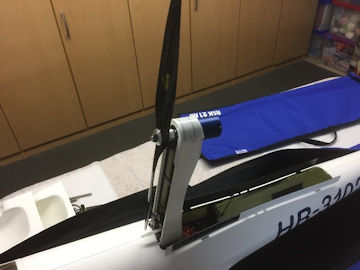 | 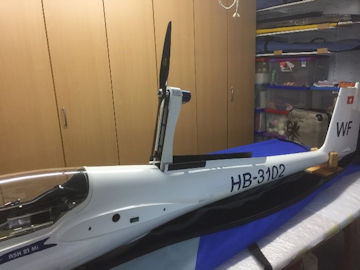 |
KTW Version v1.0 noch als Prototyp |
Akkuhalter einbauen:
- GFK Batteriebox von LET Model zusammenschneiden und verkleben.
- Auf der Unterseite GFK Verbinder und Klebsockel anbringen, damit 2 Aussparungen bleiben für die Kabelbinder.
- Moosgummi zuschneiden und in Halter einkleben.
- Akkuhalter mit 5min Epoxy mit Baumwollflocken gemischt in Rumpf einharzen.
|
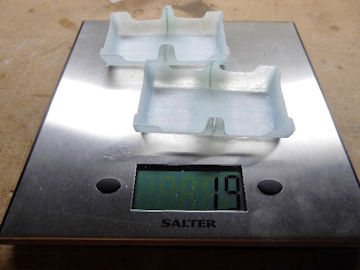 | 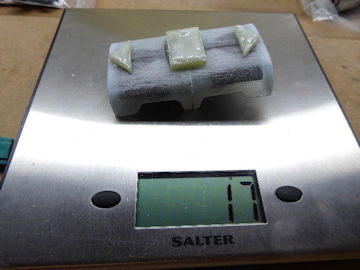 |
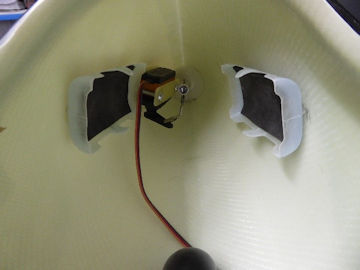 | 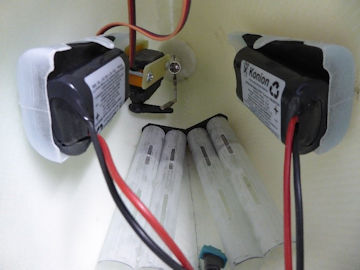 |
Ballastsystem einbauen:
- Die Nachfrage beim Publikum hat ergeben, dass rund 400g Blei in der Nase nötig wären.
- Der provisorische Modellaufbau hat gezeigt, dass es vermutlich ca. 800g Gewicht in der Rumpfspitze brauchen wird für einen Schwerpunkt von 121mm (Herstellerangabe).
- Ich nehme 4 GFK Rohre mit 18mm Innendurchmesser für die Aufnahme von bis zu 12x 100g Bleistücke, und harze die Rohre in die Rumpfspitze. Rohre und Blei bezogen von LET Model.
- Zwischen den Rohren hat es ein Fach für weiteres Trimmblei, plus vorne rechts bringe ich eine zusätzliche Trimmbleibox an.
- Der geschraubte Abschlussdeckel ist zugleich das Steckerbrett für die beiden Empfängerakkus.
- Nachsatz: Es brauchte schlussendlich 1.3kg Ballast plus rund 270g SK-Servo und Rx-Akkus in der Nase. Die rund 1kg KTW-Masse werden durch rund 1kg Antriebsakkus aufgehoben.
|
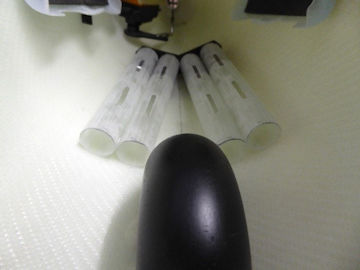 | 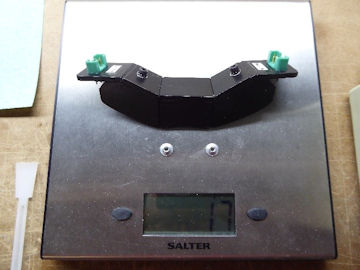 |
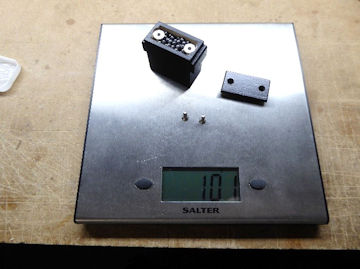 | 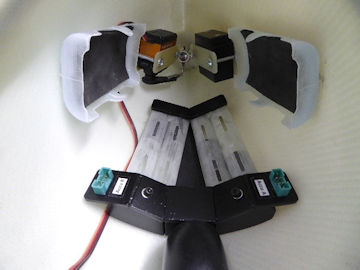 |
Haubenverriegelung herstellen:
- Hebelmechanik für die Hauben-Entriegelung/Verriegelung wie beim Vorbild für vordere und hintere Haube: 2 Griffe nach vorne drücken = Haube verriegeln, 2 Griffe nach hinten ziehen = Haube entriegeln. Die 2 Riegelstifte fahren durch den Haubenrahmen in den Kabinenbogen. Problem: An die Hebel auf der rechten Seite kommt man nicht ran, wenn die Hauben geschlossen sind. Werkseitig ist ein einfacher Stift vorgesehen, die Hauben ohne Klappmechanik.
- Erst wollte ich eine Servo getriebene Nockenscheibe links und rechts in die auszusparende Nische des Kabinenbogens einbauen, welche die vorgespannten Riegelstifte bewegen. Nach Rücksprache mit dem Hersteller würde der Kabinenbogen dadurch aber zu stark geschwächt, dort wurde nämlich für die notwendige Stabilität mit 3 Lagen CFK Rovings plus Füllmaterial (Harzgemisch mit Microballons und Baumwollflocken) aufgefüttert. Also lasse ich das bleiben.
- Dann wollte ich die rechten Hebel mit einer 0.5mm Bowdenzugverbindung zu den linken Hebel in den Haubenrahmen einlegen. Jedoch habe ich wegen der 3 engen Bögen Spiel im Bowdenzug festgestellt und das gibt am Ende wohl nicht schön schliessende oder nicht schön öffnende Riegel auf der rechten Seite. Es bräuchte eine bestimmte Zugvorspannung um das Spiel zu kompensieren, das wird wieder kompliziert. Zudem wird die Zuganlenkung asymmetrisch weil
die Hebelpunkte links und rechts nicht an der gleichen Stelle angreifen können. Dadurch wird diese Idee nochmals etwas komplexer. Die Hebelsynchronisierung ist ebenfalls schwierig einzustellen, der Zugdraht müsste verstellbar sein. Also lasse ich auch diese Idee bleiben, das muss einfacher gehen und dauerhaft halten.
- Lösung: Ich stelle ein Bedienstab mit einem Gummiende her, mit welchem ich durch die Fenster die rechten Hebel bedienen kann. Allenfalls lasse ich die Vorspannfedern im Führungszylinder auf der rechten Seite weg. Sobald die vordere Haube offen ist, kommt man bequem auch an die hinteren beiden Griffe ran.
- Zuerst Rahmenüberstand am Rumpf weggedremelt und weggeschliffen.
- Alu U-Profil für den Führungszylinder geschnitten und an der Rahmenrundung angepasst, Stellring M2 für den Anschlag der Vorspannfeder eingeharzt, Federstahldraht 2mm genommen, Feder aus Kugelschreiber als Vorspannfeder verwendet und mit Sicherungsscheibe M2 auf Federstahldraht gebracht, Messingrohr 2/3mm als Führung im Haubenrahmen. Führungszylinder mittels M3 Gewinde des Stellrings von unten her auf den Rahmen geschraubt, am Zylinderende hält es dank der Führung im Messingrohr. Alles ist nachträglich demontierbar.
- Auf der Hebelseite mittels M3 Einschlagmutter gelagert. Dort braucht es eine kleine Aussparung im Rahmenfalz des Rumpfes.
- Die 4 Hebel mit Alu und Messingprofilen zusammengeharzt (UHU 300 Endfest tempern). Die hinteren Hebel sind etwas länger als die vorderen Hebel, und sie erhalten ein Gelenk im Zugdraht. Zugweg vorne = 7mm, Zugweg hinten = 14mm bei 90° Hebelbewegung.
|
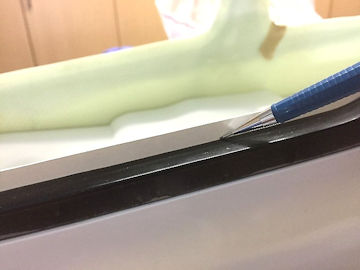 | 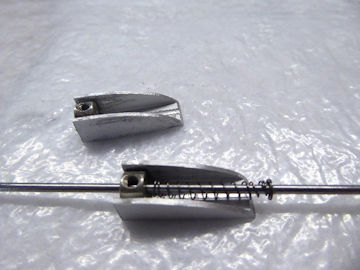 |
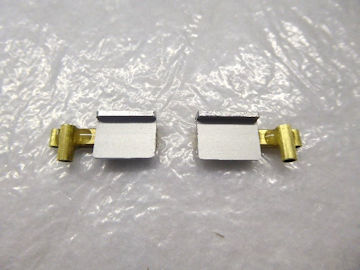 | 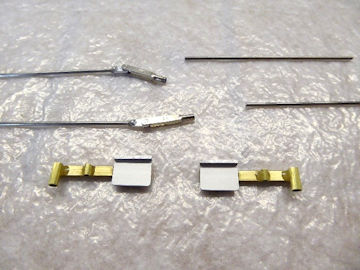 |
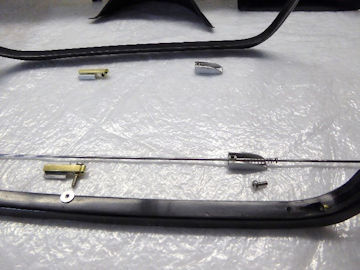 |  |
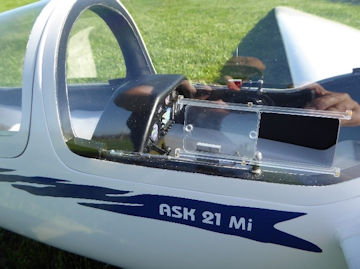 | 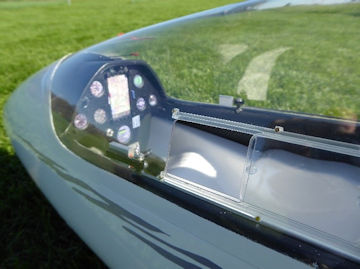 |
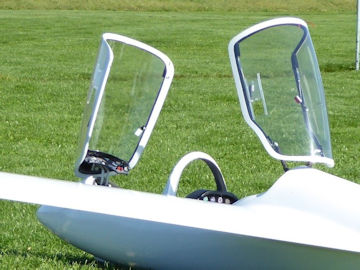 | 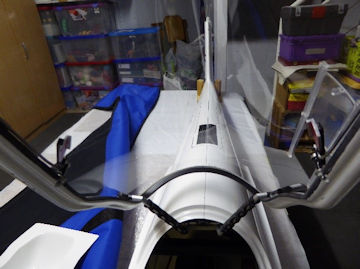 |
Haubenmechanik herstellen:
- Haubenmechanik wie beim Vorbild: Hintere Haube nach hinten aufklappbar, vordere Haube nach vorne aufklappbar. Beide öffnungswinkel an Hand der Fotos ca. 65°.
- Erwin Schreiber bietet keine Haubenmechanik mehr an für die ASK 21, deshalb Eigenbau.
- Die Bügel sind aus 6mm Alustab eloxiert hergestellt. Hinterer Bügel: Gehrungen jeweils 120° passend geschnitten und mit 2mm Draht verstiftet, danach mit UHU 300 Endfest die Gehrungen verklebt und getempert. Vorderer Bügel: gebogen und doppelt geführt.
- Das Scharnier ist ein Topfscharnier 26mm für vorliegende Türen ca. 90°, Scharnierarm und Auflage leicht modifiziert resp. eingekürzt, damit es nicht über den Bügel hinaus ragt.
- Scharnier „verkehrt“ montiert: Haube geschlossen = Scharnier gestreckt, Haube offen = Scharnier gewinkelt. Grund: Der Scharnierarm macht neben der Drehbewegung noch einen kleinen linearen Hub bei gewinkelter Stellung. Die Linearbewegung würde für den geschlossenen Zustand der Haube im Doppelfalz stören.
- Klemmplatte als Gegenplatte aus 2mm GFK hergestellt und zwei M4 Muttern eingelassen, und mit dem Bügel verklemmt. Haube kann später ausgerichtet oder abgenommen werden.
- Kleiner Spant 8mm Birkensperrholz (Abfallresten aus KTW Spant) für Topfscharnier hergestellt und die richtige Position im Rumpf herausgesucht, damit der Rahmen sauber schliesst, es in beiden Positionen eine Scharniervorspannung hat, und die Bügelposition mit der Haube zusammen am Ende noch einigermassen vorbildgerecht aussieht. Nicht ganz so einfach zu machen, es braucht etwas Geduld und Hilfsmittel und Bauprovisorien, bis die geeignete Position gefunden ist.
- Vordere Haube: Gleich modifiziertes Topfscharnier 90° wie hinten, Drehpunkt kommt ca. 40mm vor und ca. 27mm unterhalb dem Haubenrahmen zu liegen. Wie beim Original braucht es einen trapezförmigen Umlaufbügel, Befestigung unter dem Paneldach.
- öffnungswinkel der vorderen Haube ca. 65°. Scharnierarm ca. 25° vorgedreht, um ca. 65° öffnung zu erhalten. Vorspannung bei 25° immer noch gut.
|
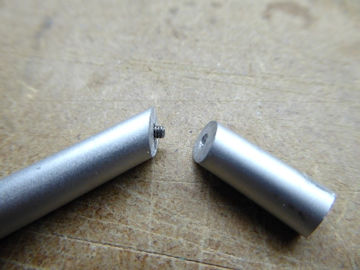 | 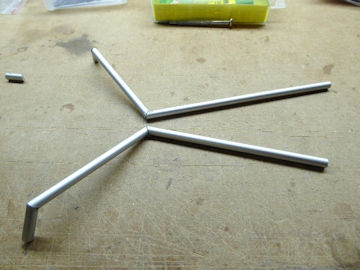 |
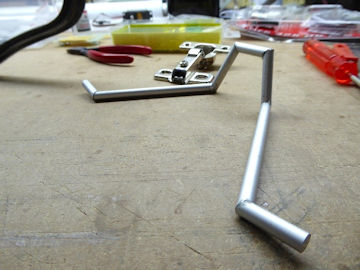 | 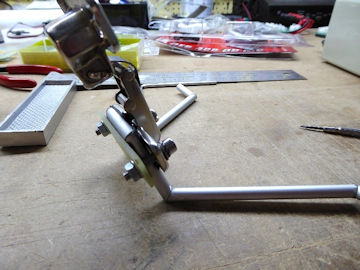 |
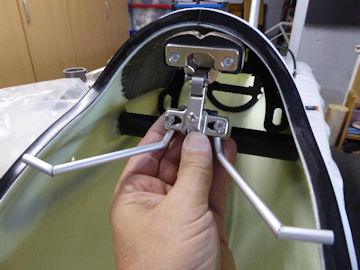 | 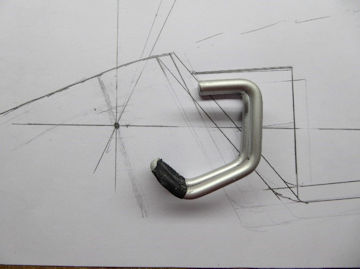 |
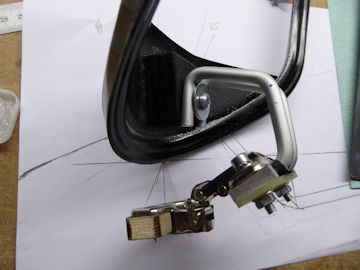 | 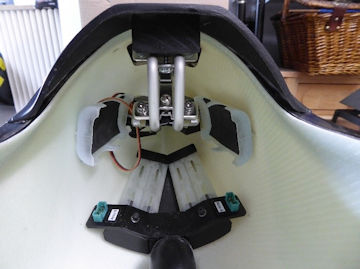 |
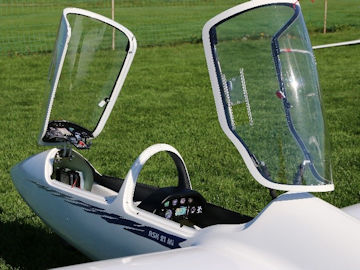 | 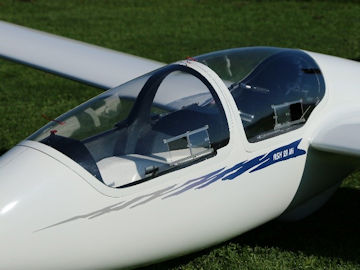 |
Sitzwannen einbauen:
- Kleines Detail: Die Sitzwannenformen sind nur vorbildähnlich hergestellt, wahrscheinlich wurden sie aus praktischen Gründen vereinfacht resp. abgeändert. Bei der vorderen Wanne fehlt der Schulterbereich, und bei der hinteren Wanne liegt der Gesässbereich zu weit hinten. Stört aber nicht gross, und ist nach dem Bau bestimmt schnell wieder vergessen. Keine Kritik, nur Notizen.
- Beide Wannen herausnehmbar, hinterer Instrumentenpilz mit 4 Magneten befestigt für leichteres Ein- und Ausbauen beider Sitzwannen.
- Pro Wanne 4 GFK Auflagen 15x25mm, Wannen werden mit Klett auf den Auflagen gesichert.
- Zum Akku-Handling und für das Binden der Empfänger reicht es, die vordere Wanne auszubauen.
- Display der PowerBox kann abgelesen werden bei eingebauten Wannen.
|
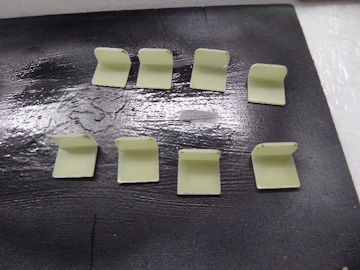 | 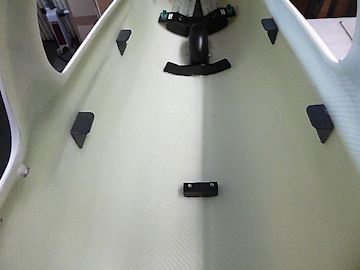 |
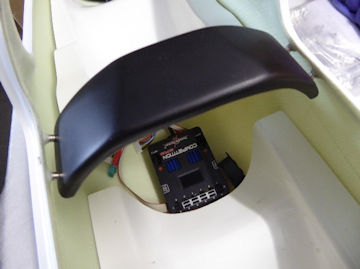 | 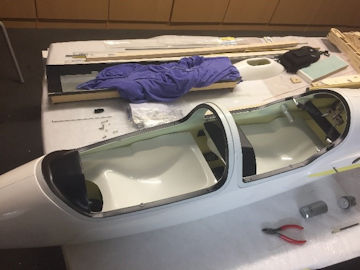 |
RC-Elektronik einbauen:
- 9x Savöx SA-1256TG @5.9V (200Ncm), 2x Quer, HR, SR, 2x Bremsklappen, SK, Radbremse, Turm.
- SK Servo und Turm Servo über 3-Weg Schalter an Merbold KTW Steuerung angeschlossen.
- 2x Empfänger Futaba R6308SBT über S-BUS redundant an PowerBox (2x 18 Kanäle redundant).
- Motorakkus mit Klett befestigt für leichtes ein- und ausbauen zum Laden. HV Serieschaltbrücke aus 2mm GFK mit 2 MPX Steckern.
- PowerPox auf 3 Holzsockel
- Beide Empfänger mit Klett, darauf geachtet dass die Bindtasten gut zugänglich bleiben und die Diversity Antennen 90° verlegt werden können.
- Regler mit Klett, darauf geachtet dass die Akkukabel nicht länger als 30cm werden.
- KTW Steuerung mit Klett, darauf geachtet dass der USB Stecker für Programmierzwecke gut zugänglich bleibt.
- GPS Sensor auf Holzsockel und Klett, darauf geachtet dass er nicht in der Nähe der Antennen ist und dass alle 3 Achsen X, Y und Z im Rumpf ausgerichtet sind. Für die Entnahme der Speicherkarte muss leider die hintere Sitzwanne herausgenommen werden, nicht so tragisch da mich die Logdaten in der Regel nur am Anfang interessieren.
- Kabel und Bowdenzug im Rumpf ausgerichtet und mit Sekundenkleber der Länge nach runterlaufen gelassen.
- Teflonschlauch für TEK im Rumpf ausgerichtet und mit Harz stellenweise fixiert (Sekundenkleber hält nicht).
|
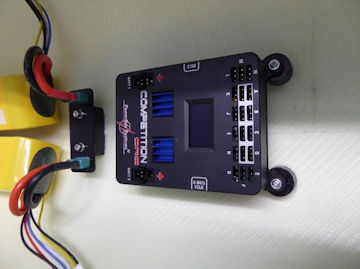 | 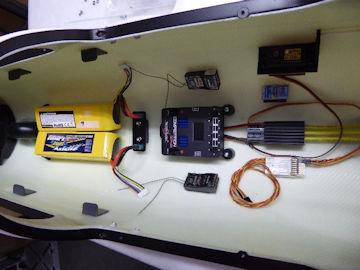 |
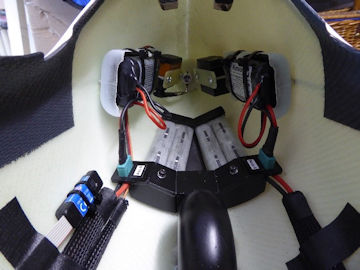 |  |
TEK-Düse einbauen:
- Düsenhalter vorderes Ende für Düsenaufnahme ist etwas dicker, Einbaurichtung beachtet.
- Düsenhalter direkt unter Servospant als Auflage für optimale Befestigung. Passt gut von der Höhenlage her. Der Rumpfmittelachse nach ausgerichtet.
|
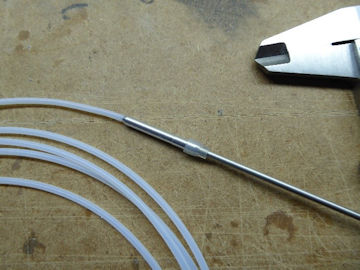 | 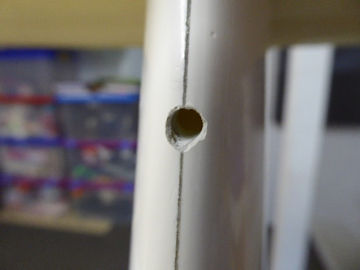 |
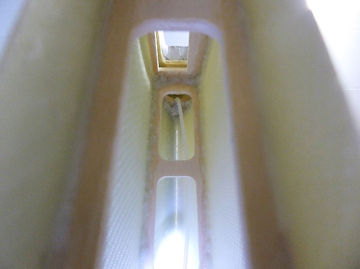 | 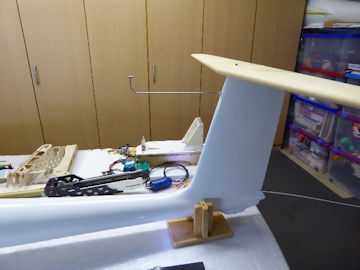 |
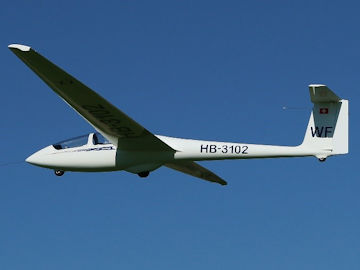 | 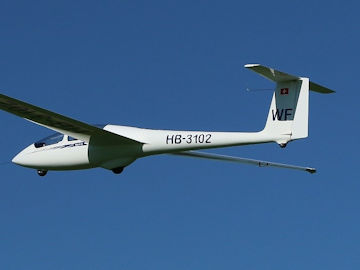 |
Randbögen herstellen:
- Originalbogen nur ca. 10mm dick, die Mi-Ausführung mit Räder müsste theoretisch etwas dicker sein. Länge ca. 50cm Höhe ca. 10.5cm, Dicke beim Rad unbekannt, vermutlich gegen 30mm. Kann ich nicht scale machen, das würde zu dünn und zu schwach werden.
- Original sind Skater Räder 80mm Durchmesser und 15mm Breite, laut Info von Sven. Ich mache 24x6mm GFK Räder, Radkasten dazu entsprechend etwas grösser 26x8mm.
- Für Randbögen Balsaleiste 30x50mm möglichst hart gewählt, auf Profil angeformt und Randbögen an Hand von Fotos angezeichnet, mit Bandschleife grob bearbeitet. Später die Kanten abgerundet und am Schluss wo nötig gespachtelt und alles lackiert.
- GFK Radkasten aus 2mm GFK Platte und 0.5mm Resten hergestellt, innen 26x7.5mm für GFK Rad 24x6mm plus U-Scheibe M2x0.3mm je Radseite zwei Stück. Lager M2 Schraube, Kontermutter fix am Radkasten aussen verklebt, dann Radkastenschacht im Randbogen ausgefräst und Radkasten in den Randbogen versenkt.
- Randbögen werden aufgesteckt mit zwei 4mm Goldkontakten, Randbögen für Transport abnehmbar. Vorgängig Lochschablone der Endrippe gefertigt. Buchse Flügelseitig, Stecker Randbogenseitig. Stecker in CFK Röhrchen 6x7mm eingelassen für besseren Halt im Balsa.
- Alles zusammen sehr viel Arbeit, aber war mir wichtig.
|
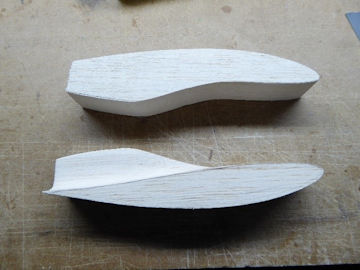 | 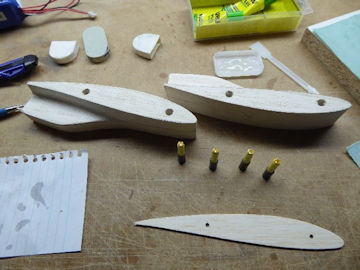 |
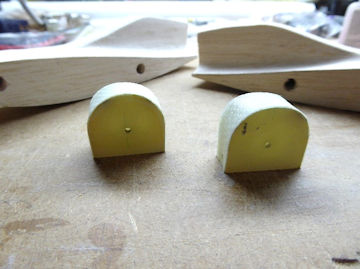 | 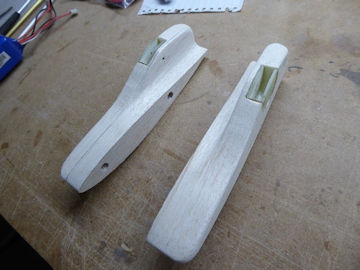 |
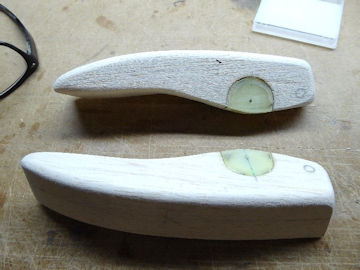 | 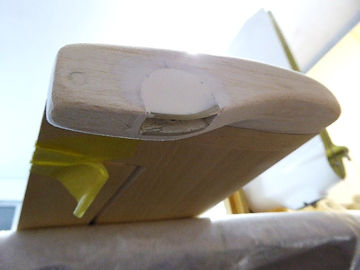 |
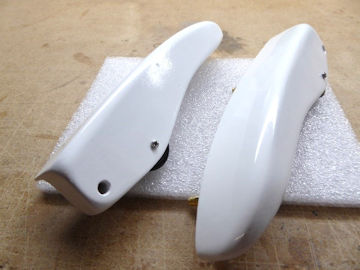 | 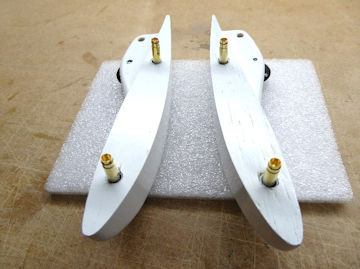 |
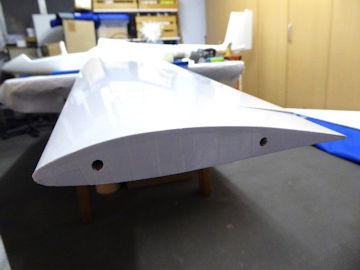 | 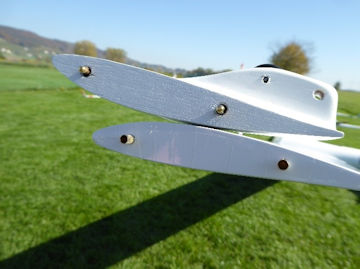 |
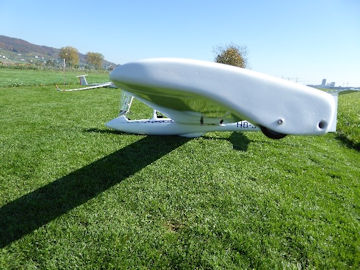 | 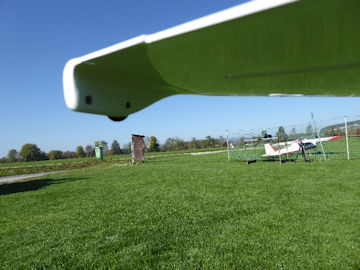 |
Flächenservos, Anlenkungen, Stecker einbauen:
- Styro ist werkseitig zu hoch belassen für meine 20mm Servos. Styro lässt sich super mit zylindrischem Schleifdremel auf die gewünschte Einbauhöhe abfräsen, und wo es am Rand mit dem Dremel unzugänglich wird, mit der heissen Lötkolbenspitze nachbearbeiten (Tipp vom Alex).
- Styro bei Bremsklappenservo auf 35mm Einbautiefe abgefräst, damit der Servohebel verschwinden kann. Beim Querruderservo sind es 20mm Einbautiefe, hier kommt dann teils grad die Oberschale zum Vorschein. Styro soweit plangefräst, bis das Querruder Servo rundum bündig mit der Auflage der Abdeckplatte ist.
- 3mm Birken-Sperrholz Grundplatte 50x70mm auf Styro resp. Oberschale geklebt für festen Untergrund, dann mit hölzernen Servohaltern auf der Grundplatte, seitlich und mit der Auflage der Abdeckplatte mit Epoxy verbunden. Darauf geachtet, dass die Grundplatte gerade ausgerichtet ist zur Servoabdeckung, weil diese später plan auf das Servo drückt.
- Die Servoabdeckung für das Bremsklappenservo erhält ein Andrückklotz, weil das Servo 15mm tiefer liegt.
- Alles passgenau hergestellt und es sind keine extra Servoschrauben nötig, die 4 Schrauben der Abdeckung reichen vollends aus für einen top festen Servositz.
- Beim Linken Querruder Servo vorne 2mm zu viel Styro ausgedremelt (22mm statt 20mm). Grundplatte mit 2mm Spachtelmasse unterfüttert, 7g Mehrgewicht, schadet aber nix weil die linke Fläche eh 60g leichter ist als die rechte Fläche.
- Spezialwerkzeug hergestellt zur bedarfsweise Entnahme der eingepressten Servos.
- Anlenkungen Bremsklappe werkseitig vorgegeben mit 2.5mm Gabelkopf.
- Anlenkungen Querruder mit 3mm Gabelkopf, und die mitgelieferten GFK Ruderhörner verwendet und fluchtend eingeklebt.
- Die 2-stöckigen Bremsklappen 450/57mm von Schambeck haben eine Top Qualität und laufen fast spielfrei. Sehr solide Feinmechanik. Die Klappenverriegelung rastet gut hörbar ein, grosse Hilfe beim Servo einstellen. Servoweg ca. 25mm erfordert ein mittelgrosses Ruderhorn, das ist bei der Servo Einbautiefe vorab berücksichtigt. Die Einbauanleitung von Schambeck wurde komplett berücksichtig (Servoeinbaurichtung, Servokräfte, Verriegelung auf Totpunkt). Die Sache mit dem Totpunkt wurde zuerst nicht beachtet, das bescherte zunächst heiss laufende Servos bei eingefahrenen Bremsklappen. Das wurde aber korrigiert, jetzt ist das Servo ruhig und bleibt kalt.
- Flächensteckverbinder MPX grün 6-pol, Flächenseitig = male und Rumpfseitig = female. Flächenseitig ist ein Einbaurahmen vorgesehen (Aussparung ist werkseitig bereits passend gefräst). Lose Kabelenden an der Flächenwurzel könnten ohnehin nicht in den Styrokanal zurück geschoben werden, wenn die Fläche aufgesteckt wird. Dafür ist der Kanal zu eng, und ich mag grundsätzlich auch keine bewegten Kabel. Rumpfseitig muss der MPX Stecker Rahmen 2mm vom Rumpfanschluss abgesetzt werden, um genügend guten Kontakt herzustellen (Abachibeplankung steht etwas vor).
- Anlenkung HR mit M3 Gabelkopf. Gewindestange M3 läuft schräg um die Befestigungsschraube M5 vom HLW und schräg nach oben zum HR zur Augenschraube M4
- Anlenkung SR Bowdenzuggestänge servoseitig mit Z eingehängt und Ruderseitig mit Gabelkopf M2.5 in Augenschraube M4.
|
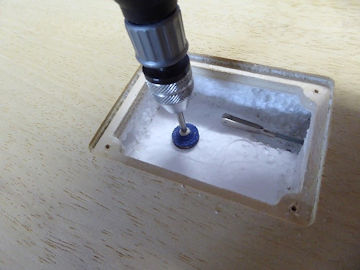 | 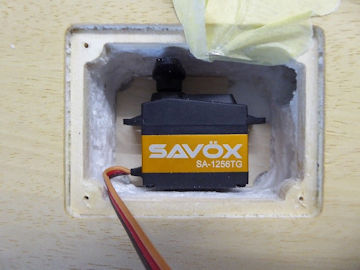 |
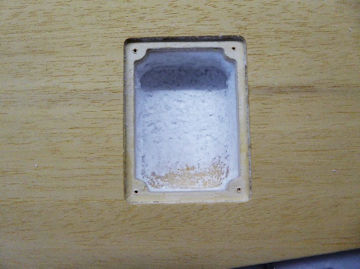 | 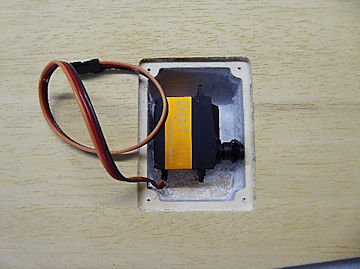 |
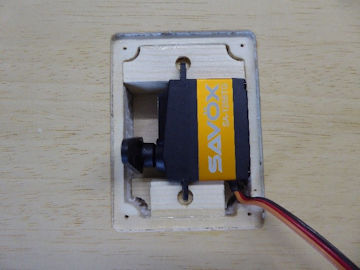 |  |
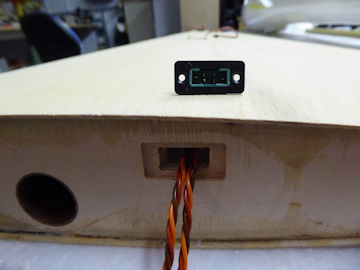 | 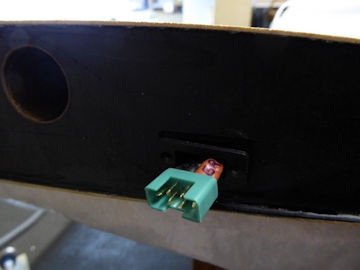 |
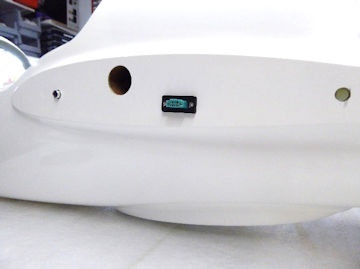 | 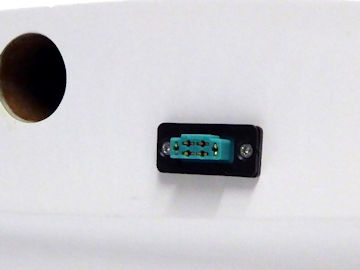 |
Monoblocks einbauen:
- Werkseitig sind M6 Rändelschrauben zur Flächensicherung vorgesehen.
- Ich mag auf dem Platz nicht rändeln und ersetze die Schrauben durch Monoblocks. Gewindestifte dazu sind leider M4.
- Zwei Adapter gedreht von M4 auf M6
- Block mit Endfest bestrichen und Gewindestift mit blauem Loctite bestrichen. Stift wenige mm in Fläche angesetzt. Dann Fläche an Rumpf geschoben und Block auf Stift geschnappt. Dann den Block mit dem Stift zusammen solange gedreht, bis rumpfinnenseitig anliegend.
|
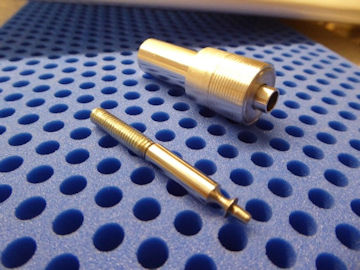 | 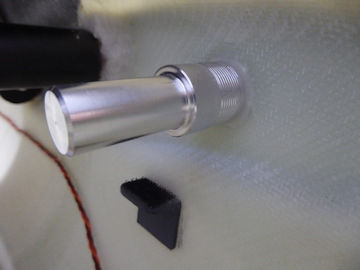 |
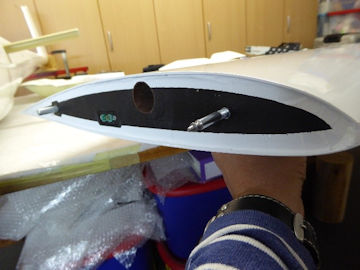 | 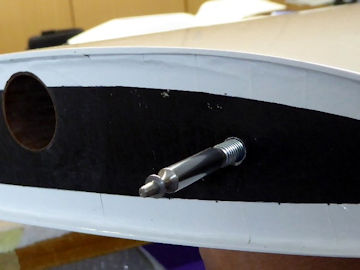 |
Flächen folieren:
- Orastick Weiss 25-010-010 genommen, Montageanleitung von Lanitz-Prena Folien Factory GmbH seriös befolgt. Hinweise zur Empfangsreduktion bei SCALE- und CHROM-Farben beachtet.
- Stick statt Cover genommen auf Anraten von Jürg Vetterli, und weil meine Tests ergeben haben, dass Stick etwas weniger schrumpfempfindlich ist und dann auch weniger schnell faltet und Blasen bildet als Cover. Konnte Stick einfacher zuschneiden als Cover, weil bei Cover die Trägerfolie ständig verrutscht (das nervte mich vielleicht). Konnte Stick auf den kleineren und mittelgrossen Flächen besser anbringen (zu zweit) als Cover, und man muss sich beim Bügeln nur noch aufs Bügeln konzentrieren und nicht auch noch auf die Ausrichtung der Folie. Nachteil von Stick sind die haftenden überstände, auf die man achten muss, dass sie nicht zufällig irgendwo ankleben. Stick Weiss ist 92g/m2, Cover Weiss wäre 89g/m2.
- Standard Weiss statt SCALE-Weiss genommen, weil die rückseitig bedampfte Alu Nanoschicht bei den SCALE-Farben die 2.4GHz Empfangsanlage empfindlich stören kann, auch wenn die Antennen im GFK Rumpf verbaut sind und die SCALE-Folien nicht direkt einen Faradayschen Käfig um die Antennen bilden. Allerdings würde SCALE-Weiss besser decken als Standard Weiss, hätte mir von da her besser gefallen. Jedoch hat SCALE-Weiss einen ganz leichten graublau Stich vom Alu und wirkt etwas kühler oder frischer als Standard Weiss. Das Standard Weiss wirkt etwas süffiger und wärmer. Beide Farbtöne passen relativ gut zum Rumpf, SCALE-Weiss hätte noch einen Tick besser gepasst, aber die Empfangssicherheit ist mir wichtiger.
- Flächen auf Anraten von RCN User „Uhu“ mit Clou Schnellschleifgrund G1 (300) 1x versiegelt und verschliffen und entstaubt. Der Fläche links hatte ich deutlich mehr Material aufgetragen (2x versiegelt), um den Gewichtsausgleich zu Rechts etwas zu kompensieren (Schon beim Einbau Flächenservos etwas Gewicht kompensiert). Der befürchtete Holzverzug auf Grund je einseitiger Behandlung hat sich überhaupt nicht bestätigt. Die Ruder und Endleisten sind nach wie vor top gerade, null Verzug.
- Erst hatte ich Oracover Heisssiegellack auf einem Muster von Marcel getestet, und nicht bedacht, dass der Heisssiegellack als Haftgrund für nicht tragfähige Materialien (wie z.B.: sehr poröses und faseriges Balsa) vorgesehen ist, dessen Fasern den Folienkleber schlecht tragen. Das hat aber den Nachteil, dass späteres Feinschleifen der Oberfläche im Haftgrund hängen bleibt und als Staub zurückbleibt, das ist natürlich unbrauchbar für meine Anwendung.
- Nach 1 Tag Trocknung mit 800er Papier und nicht zu starkem Druck feingeschliffen. Es braucht nicht viel Druck und nicht viel Zeit, bis die Oberfläche wieder glatt und hell wird. Danach komplett entstaubt mit Sauger und Pinseldüse, sowie teils Pressluftpistole (Kompressor ist mir kaputt gegangen) oder leicht feuchter Mikrofaserlappen. Staubtest: Hände spülen und abtrocknen, danach mit Handfläche über Oberfläche fahren. Wenn die Handfläche leicht weiss wird, ist noch Staub in den Abachiritzen. Das muss raus.
- Querruder bei der Verkastung um 1mm abgeschliffen, das ist das Spaltmass für das spätere Silikonscharnier plus die Foliendicken. Höhenruder Aussparung für SLW ebenfalls die 1mm einberechnet.
- Seitliche Verkastungen bei Querruder und dessen Flächenaussparung glatt gespachtelt, damit Folie besser hält.
- Am Schluss nach dem Folieren die 2 Augenschrauben M4 für das HLW und SLW sowie die 2 werkseitig gelieferten GFK Ruderhörner für die Querruder mit Epoxy eingeklebt.
- Am Folieren habe ich keinen Spass, egal ob Stick oder Cover. Alleine mit nur 2 Händen gehen die mittelgrossen und grossen Flächen praktisch kaum zum schön verarbeiten, es braucht 4 und zeitweise sogar 6 Hände dazu (2 Hände halten die Folienrolle, 2 Hände halten das Bauteil, 2 Hände folieren).
- Querruder: Die sind erfreulicherweise sehr gut zum Folieren gegangen, gerade Kanten und keine Rundungen, das geht prima auch alleine. Nur zum Aufziehen des Streifens zu zweit.
- Seitenleitwerk und Höhenruder: Bei den Rundungen des SLW und den runden Aussparungen des HR ist es nicht so schön geworden. Es hat dort etwas Falten gegeben, und die Kontur ist dort teils unstetig geworden. Das sind meines Erachtens die schwierigsten Teile.
- Höhenleitwerk: ähnlich gut gegangen wie bei den Querrudern. Die konvexe Fläche ist für die Folie kein Problem, allfällige Rümpfe auf Grund der bombierten Oberfläche lassen sich schon vor dem Bügeln ausstreichen. Die Randböglein habe ich die Folie gezogen und gewärmt und gezogen, dann das überstehende Gewurstel abgeschnitten. Dann die Restfalten mit einer höheren Bügelstufe glattgebügelt. Die Falten sind aber dort nicht ganz verschwunden.
- Flächen: Die Befürchtung um Verarbeitungsprobleme auf Grund der konvexen und konkaven Oberfläche auf der Flächenunterseite quer zur Abrollrichtung der Folie hat sich überhaupt nicht bestätigt. Die Folie konnte zu zweit in nur 5min falten- und blasenfrei aufgebracht werden, es ist wieder etwas Freude zurückgekehrt. Die Abschlüsse ab der Wurzel und am Rand habe ich bei der Rundung Stück und Stück eingeschnitten und angebügelt, sieht sehr gut aus. Als Antirutsch wurden 2 Schaumstoffunterlagen auf den Tisch gelegt, wo dann der Flügel draufgelegt wird.
- Der Farbton vom Rumpf ist bei Tageslicht nun doch auffällig anders als die grossflächige Folie. Ich müsste fast den Rumpf lackieren, das unterlasse ich definitiv. Was soll’s, fliegen wird’s trotzdem. Vielleicht ist’s mein Erster und Letzter Styro-Abachi Baukasten...
|
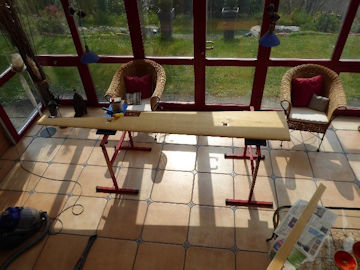 |  |
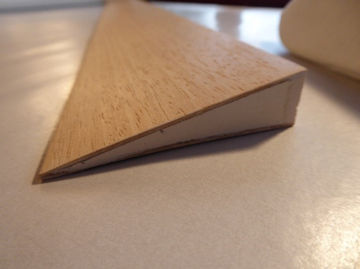 | 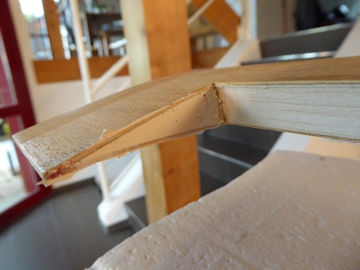 |
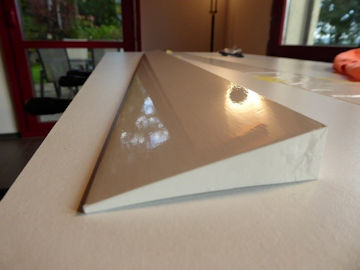 | 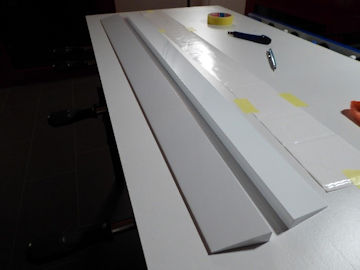 |
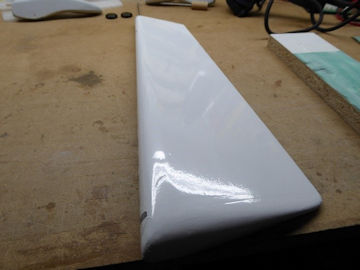 | 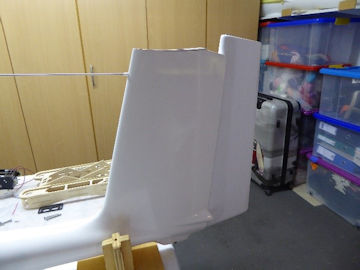 |
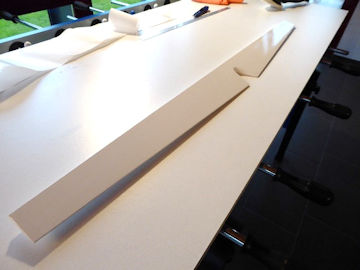 | 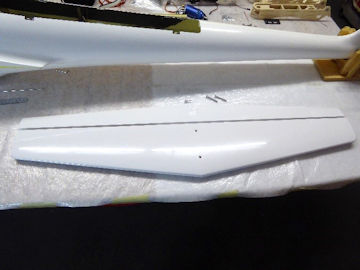 |
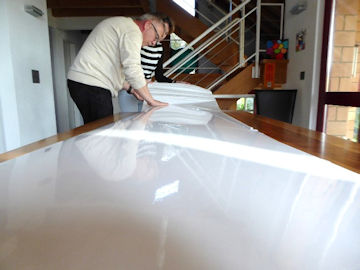 | 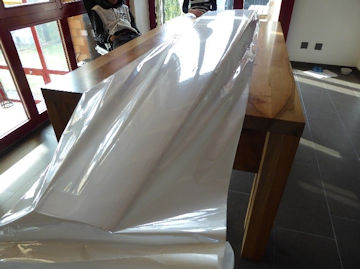 |
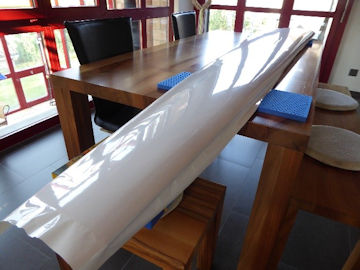 | 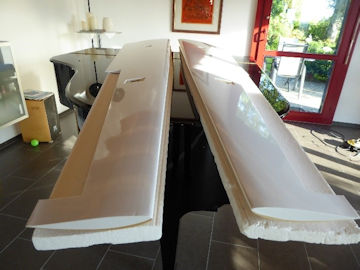 |
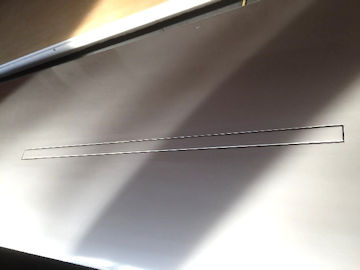 | 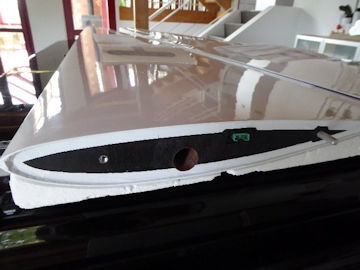 |
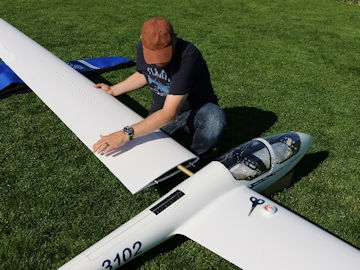 | 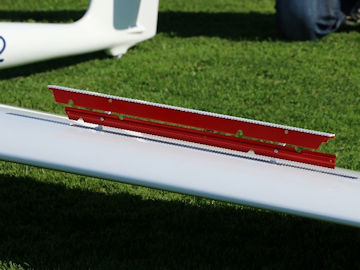 |
Ruder anscharnieren:
- Anleitung von Suter Swiss Composites befolgt.
- Silikon Elastosil E41.
- Spritze Kanüle 1.2mm, Raupe gelegt und dann mit Kanülenrücken und mit nur dem Eigengewicht der Spritze den Spalt abgezogen. Die 0.8mm Kanüle ist definitiv zu dünn.
- Silikonkanten mit 800er Schleifpapier vorgängig angeraut
- 4 Tage Austrocknungszeit
- Ergebnis sehr zufriedenstellend. Leichtgängige Scharniere, teils nur zwei bis höchstens 3 minimale Lunkern von 3-4mm Länge. Die habe ich problemlos nachgebessert, sieht gut aus und hält prima.
|
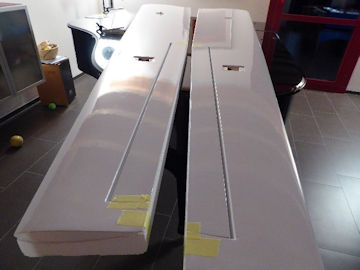 | 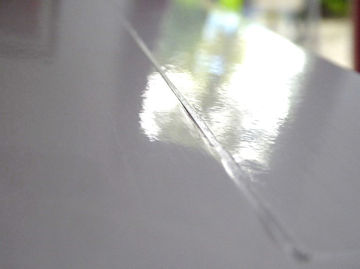 |
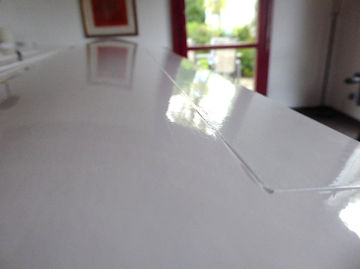 | 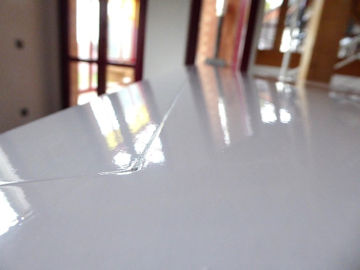 |
Cockpit Panels einbauen:
- Cockpit Panels von Pavol Sloviak Scale-Cockpits
- 57er und 80er Instrumente im Massstab 1:3.3 nicht verfügbar, wir müssen tricksen
- Beide Panels mache ich abschraubbar, vor allem vorne kann man dann besser die Haubenmechanik montieren und einstellen.
- Hauben Notabwurf mit 1mm und 2mm GFK Resten hergestellt.
|
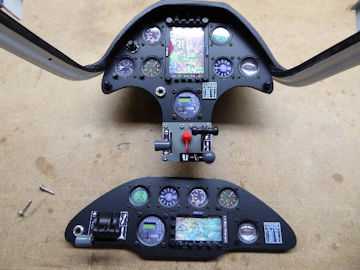 | 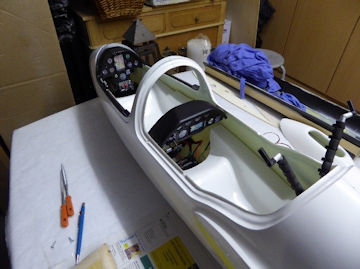 |
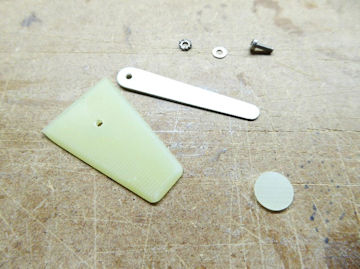 | 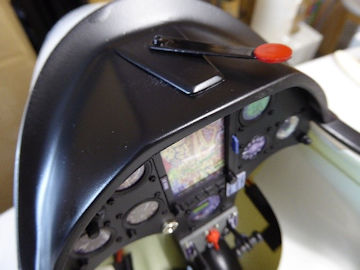 |
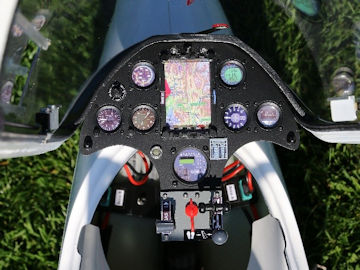 | 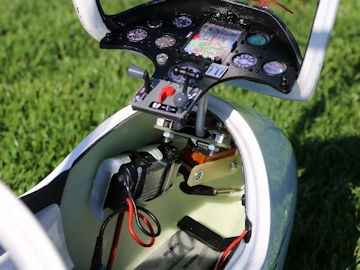 |
Haubengläser aufkleben:
- Die Haubenrahmen passen im Bereich der Rahmenbögen nicht auf die Haubengläser. Die Bögen liegen nur mit der Kante anstatt mit der ganzen Rahmenfläche auf dem Glas. Die alten Formen für die Haubenrahmen geben keine fertige Schräge für das Haubenglas her. Ich muss die Rahmen passend schleifen.
- Die Haubenrahmen stehen teils zu weit über den Kabinenfalz. Auch dort muss ich die Haubenrahmen passend schleifen. Foliendicke der Haubengläser ist 0.8mm, dieses Mass habe ich in Minimum eingehalten, damit die Haube nirgends übersteht. Wirklich viel Arbeit, um alles anzupassen.
- Blöd ist, dass ich all das erst bemerkte, nach dem ich die Haubenverriegelungen und vorne auch den Instrumentenpilz schon fixfertig gesetzt und eingestellt hatte, und die Haubenrahmen schon vorlackiert hatte. Habe überhaupt keine Lust, das alles wieder zu demontieren.
- Gut ist, dass ich all das schon jetzt bemerke, bevor ich die Haubengläser fixfertig verklebt und lackiert habe und dann feststelle, dass es nicht gut passt.
- Am besten wär’s gewesen, wenn die sechs oder sieben knackigsten Punkte der gelieferten Bauteile auf einer A4-Seite irgendwo gestanden hätten, wozu wohl welche Bauteile vom Hersteller wie angedacht sind und unter welchen Bedingungen wie verwendet werden können. Nicht meckern, ich habe schliesslich einen Top-Bausupport von Alex.
- Haubenglas-Einheit beim Bund zerteilt und die Rahmen in ihre Glashälften gelegt und grob angezeichnet, Rahmenabstand ca. 10mm. Danach mit Dremel grob ausgeschnitten. Geht prima und schnell.
- Dann den Schnittkanten entlang auf der Glasinnenseite Klebband aufgebracht, Rahmen eingelegt und fixiert. Mit Filzstift dem Rahmenrand entlang die Kontur auf das Klebband übertragen, Filz leicht schräg gehalten um ca. 0.5mm – 0.8mm übermass zu erhalten. Dann mit Bandschleife bis zum Filzstiftrand hin abgeschliffen. Dort wo der Rahmen mehr als 1mm Spalt zum Kabinenfalz hat, entsprechend mehr Glas zugegeben bis hin zu 3mm übermass (z.B. beim Kabinenbogen).
- Schlussendlich von Hand die letzten Zehntel mm passend geschliffen. Glasränder auf Innenseite mit Cutter abgezogen.
- Rahmen zusammen mit Haubenmechanik wieder auf Rumpf montiert und Gläser mit Canopy Glue Formula 560 auf Rahmen geklebt.
- Nach Trocknung die Hauben demontiert, Glasränder aussen lackiert RAL 9016 und Transparentlack und alles wieder zusammengebaut. Insgesamt sehr viel Arbeit.
|
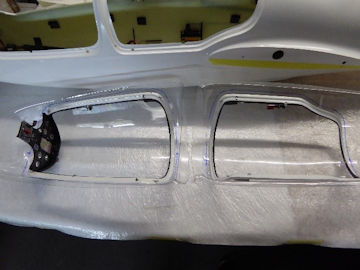 | 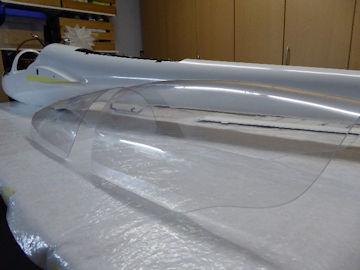 |
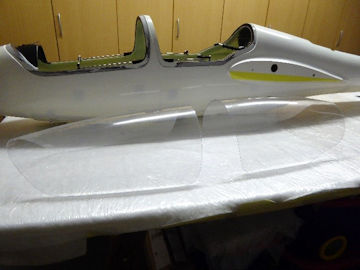 | 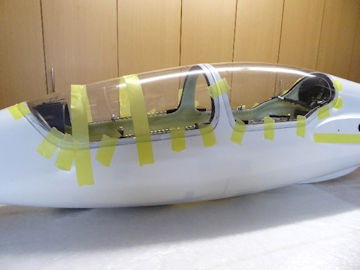 |
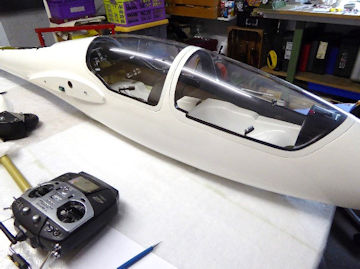 |  |
Fenster einbauen:
- Vorderes Fenster öffnet nach hinten, hinteres Fenster öffnet nach vorne.
- Fensterrahmenprofil U-Form hält den Fensterschieber in der geöffneten Fensterposition, und die schmalere L-Form hält den Fensterschieber in der geschlossenen Fensterposition.
- Gewinde M1 in Fensterrahmen geschnitten.
- Rahmenabstand mit 2 Fensterschieber gemacht und Rahmen auf Glasinnenseite vorbildgerecht positioniert und danach fixiert. Nachher von aussen mit 1mm Bohrer auf die sechs M1 Gewinde gezielt und Glas durchgebohrt. So erhalte ich keine klemmenden Fensterschieber mehr.
- Senklöcher mit Bohrer 1.5mm hergestellt.
- Rahmen mit Fensterschieber eingebaut und Glasöffnung angezeichnet. Beim Anzeichnen darauf geachtet, dass der Fensterschieber nicht durchfallen kann. Der Schieber zeigt den Falz für die Schnittlinie sehr gut an.
- Glasöffnung mit Dremel grob ausgeschnitten und mit Feile fein nachbearbeitet.
|
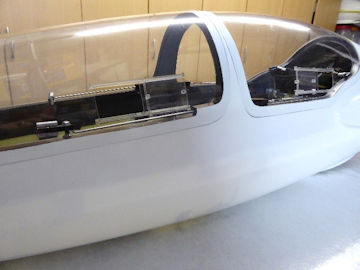 | 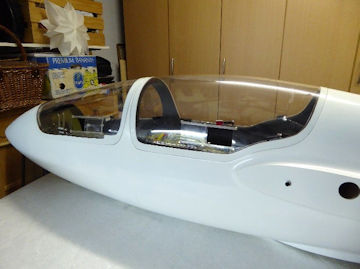 |
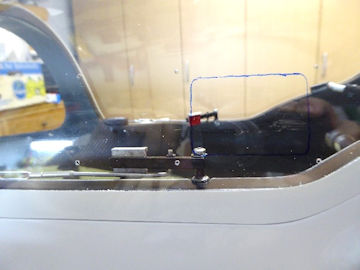 | 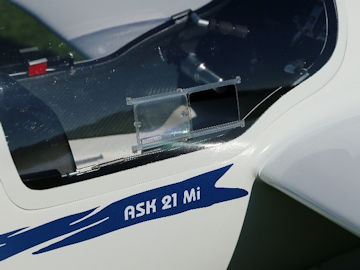 |
Ruder Ausschläge:
- Herstellerempfehlung = „Alles was geht, dann nach und nach anpassen (zurücknehmen resp. Expo einstellen usw.)“.
- Für den Erstflug habe ich es wie folgt eingestellt:
- Quer = +/-26mm, 50% differenziert für Normal- oder Thermikflug, 0% differenziert für Speedflug.
- Höhe = +/- 24mm, das wird wohl zu viel sein, habe mal Expo 25% draufgegeben.
- Seite = +/- 40mm, mehr geht leider nicht, Expo 25%.
- Bremsklappen = 0…57mm über Stick J2 und nur in Landephase.
- Radbremse = greift ab 75% Butterfly und nur in Landephase.
- Radnotbremse = über linkes Seitenpoti zur Kanaltrimmung.
|
Erstflug:
- Wieder eine sehr geile Maschine mehr in meinem Hangar...!
- Fliegt sehr schön, gleitet herrlich, super Flugbild und läuft wie auf Schienen.
- Zum Schleppen ein Traum, kommt früh vom Boden weg und bleibt fast gratis ohne viel Zutun hinter der Schleppmaschine.
- Zum Landen sehr einfach, kein gieren und kein nicken trotz deutlichem Seitenrudereinsatz und starkem Bremsklappeneinsatz.
- Bremsklappen 57mm wirken gut, aber sind nicht wie anfänglich befürchtet überdimensioniert. Jedoch mit der nötigen Vorsicht voll ausfahren, die Verwirbelungen wirken deutlich auf die Leitwerke.
- Leider hat’s mir das Fahrwerk beim Aufsetzen eingedrückt, obschon ich gar nicht mal so schlecht gelandet bin. Die 15.7kg drücken halt beim Aufsetzen direkt auf das ungedämpfte Fahrwerk. Ich muss das deutlich besser einkleben.
- Den Abfangbogen / EWD muss ich ein andermal austesten, ich konnte nur 1 Flug absolvieren.
- Auch das KTW wird erst getestet, wenn alles top eingestellt ist. Von da her ist erst der halbe Projekterfolg verbucht, aber das wird schon.
- Das komplette Set hat Platz im Opel Corsa, dieses Ziel ist ebenfalls erreicht.
- Auffällig war noch, dass das Heck in der Luft ist, wenn der Flieger ruht. War mir bis dahin nicht bewusst, aber ist eigentlich logisch auf Grund des Radstandes und der Massenverteilung.
|
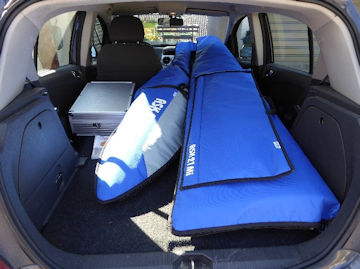 | 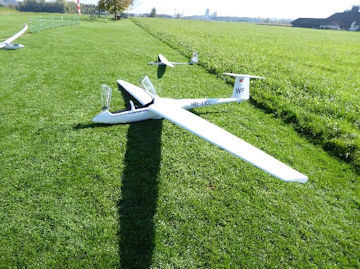 |
Dank:
- Alex Braun für das Rumpfsegment zum Testen sowie den reich bebilderten und sehr gut funktionierenden Bausupport. Sehr empfehlenswert und jederzeit gerne wieder!
- Caroline Menzi für die Vorführung des Modells.
- Jürg Vetterli für die Begleitung und Beratung beim Kauf und für die vielen Tipps zum Bau, insbesondere auch den Tipp mit dem Orastick.
- Thomas Gloor fur die Herstellung meiner unendlich vielen Frasteilesatzen zu den verschiedenen KTW Versionen und den KTW Spanten. Die Version v2 ist schon in Planung...
- René Hurschler für die Leihgabe seiner wertvollen Fein Oszillationssäge und den vielen Bautipps.
- Roman De Martin für die Bildervorlagen auf swissrumpf.ch. Es gibt ja nicht allzu viel Material im Netz von diesem schönen Flieger.
- Sven Rüssel für das nette Beratungsgespräch zu den Flugeigenschaften seiner ASK 21 Mi und den direkten Vergleich von einzelnen Themen zu seiner gleichnamigen manntragenden Maschine.
- Marcel Schneider für das Flächenmuster als übungszweck zum Folieren, und die Hilfe zu den Schwerpunkt- und EWD-Fragen sowie den schönen Fotos vom Erstflugtag, welche hier mitunter abgebildet sind.
- RCN Benutzer Uhu für den Tipp mit dem Clou G1 (300) Schnellschleifgrund, die Flächen sind wirklich Top geworden!
- Dr. Helmut Quabeck zum Thema Turbulatoren, welche ich Dank seinen Begründungen schlussendlich weggelassen habe.
|
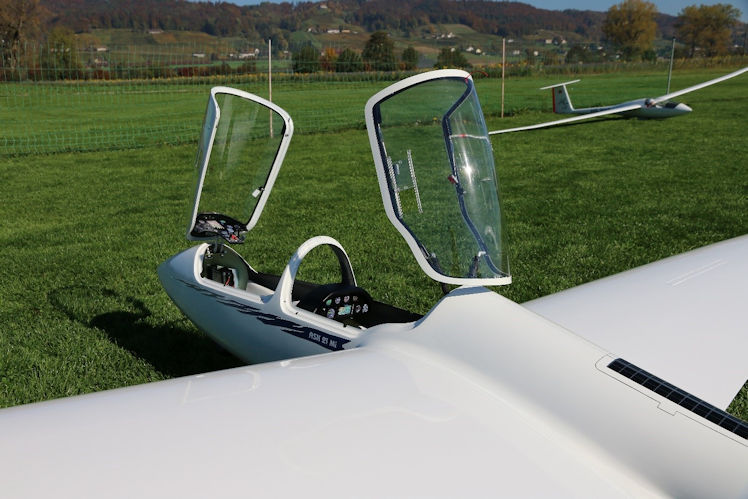 |
Technische Daten:
|
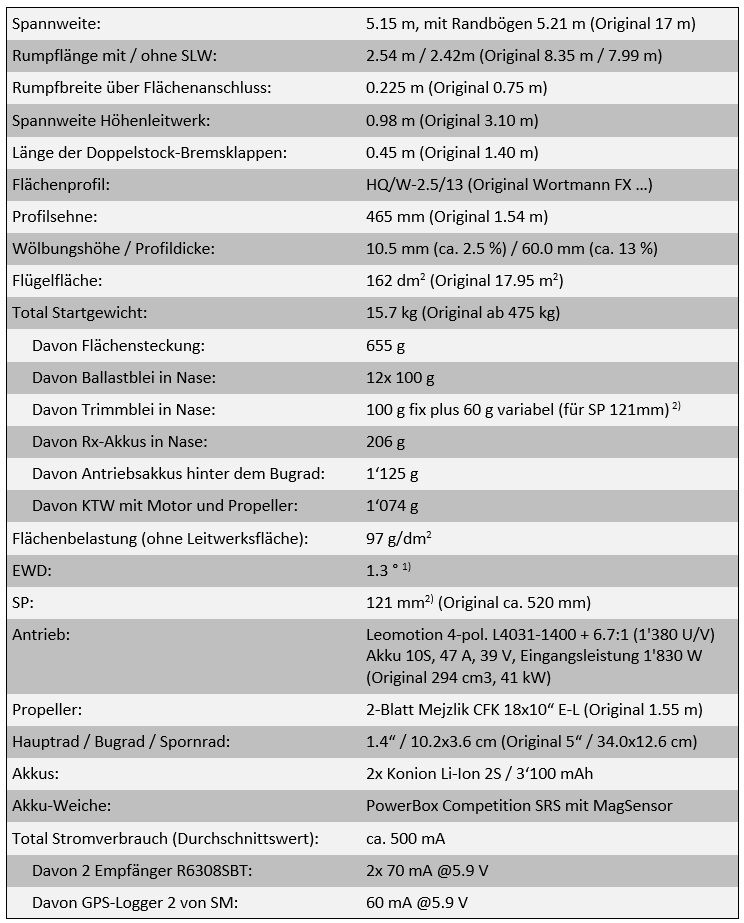 |
1) Nach der Baufertigstellung stellte sich eine EWD von 2.2° heraus. Ich lasse es so für den Erstflug. |
2) SP-Verschiebung ca. 20g/mm. Für den Erstflug mit 125mm statt 121mm geflogen, also kein variables Trimmblei mehr dazu benutzt. Sven fliegt sie mit 142mm SP. |